Automating Safety
As the overly-used phrase so correctly states: “safety is no accident”. Dedication to safety-first culture will have fewer accidents. Reduction in accidents is also the proverbial “tip of the iceberg”. A safety-first culture not only reduces accidents, but it also has numerous other major operational, cultural and financial benefits. Beyond the physical and mental suffering that an accident inflicts on the person involved, nothing can drag down the morale of the team quicker. Using software to complement safety initiatives is smart and effective, and it will also have significant cultural and financial benefits to your organization.
OSHA – friend or foe?
Is OSHA your friend? It depends on how good your safety programs are running, but it should be! The US Occupational Safety & Health Administration (if you are elsewhere, you have your own similar administration) mission statement: To ensure safe and healthful working conditions for workers by setting and enforcing standards and by providing training, outreach, education and assistance. Who would not want this? Unfortunately, many equate OSHA (and likely other regulatory compliance) as paperwork and hassle, but this should not be the attitude. I can safely say this, no one wants a visit from OSHA for a preventable accident. The costs can be significant, both direct and indirect. Below are the current OSHA-specific penalties. As you can see, this can be significant, especially for those who do not take safety seriously.
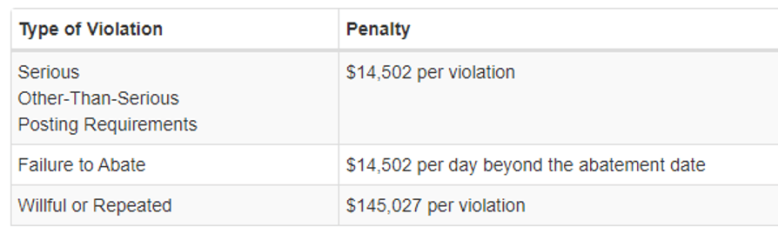
Even worse, violators suffer even greater penalties – some easily calculated, some less so. The highest cost is loss of business opportunity. This is a financial and reputation cost. There are more specific costs:
- Cost of correcting hazards
- Liability, litigation and indemnification
- Additional regulatory investigation and enforcement action (EPA for example)
- Training, process and other improvement costs
These costs can easily exceed the original OSHA violations, making safety not only the right thing to do, but the right financial thing to do as well.
Looking more closely at statistics/data around safety in the workplace…
Most Common Violations:
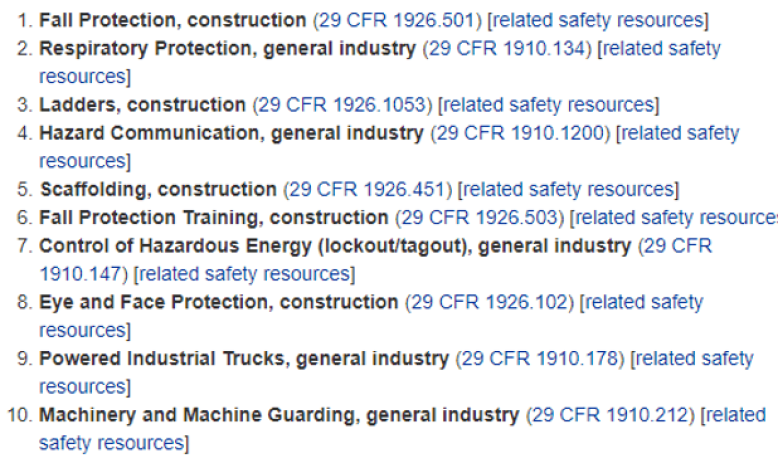
Common Workplace Safety Statistics
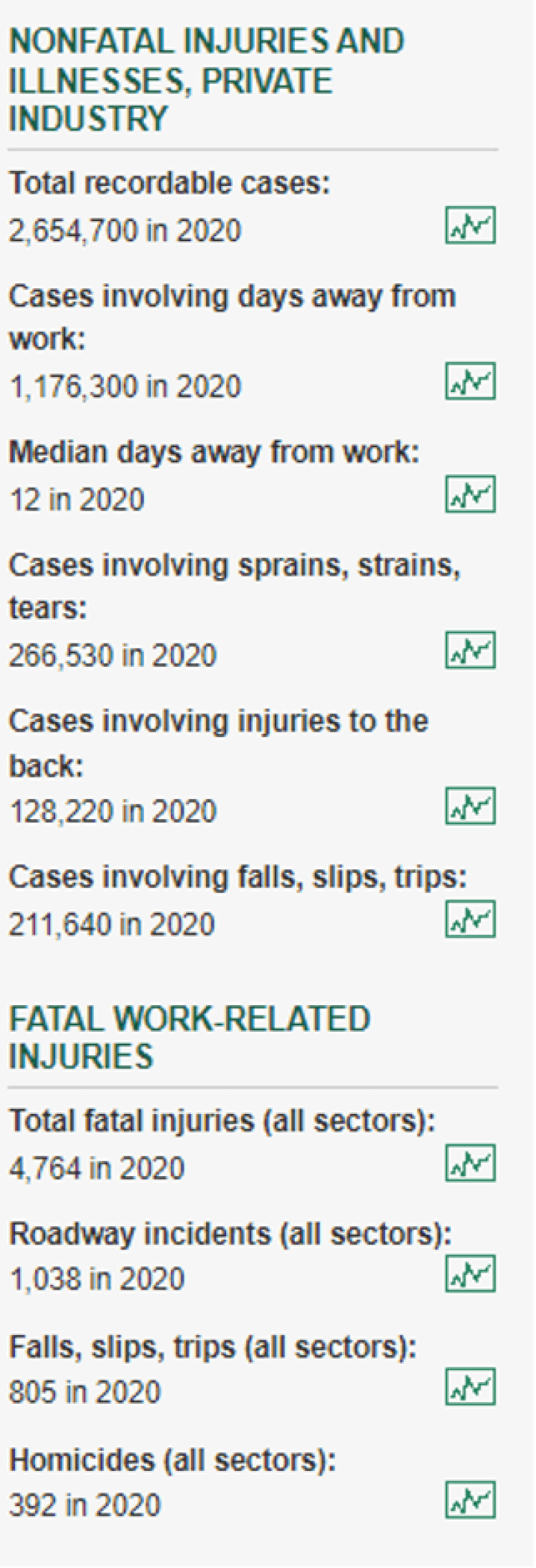
The good news is that the data is improving: the workplace is safer (statistically speaking) than in the past. Organizations understand that a safety-first culture is important. OSHA has been around for more than 50 years, helping drive safer workplaces.
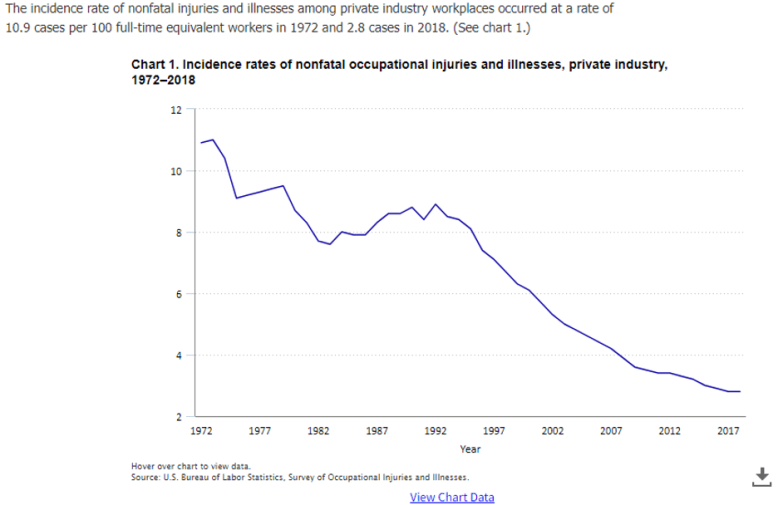
The costs to our operations are significant – adding up to $164 billion in 2020.
Can we do better? Yes, we certainly can. No matter the statistics and perceived paperwork/administrative hassle, we all agree that OSHA’s mission aligns with what today’s organization must provide: a safe workplace for our teams.
Automating Safety
Before you think about using software and other technology to improve safety-related incidents in your workplace, you must look at the people and culture first. Improving safety starts at the top of the organization and flows down to everyone and at all levels of the org-chart. Management must embrace, invest and evangelize in a safety-first culture. It is the right thing to do, and it is better for business/operations. Teams must also embrace and accept that the bravado-days, where a worker might climb a high-wire type circus ladder to change a lightbulb, are a thing of the past. While you may be able to scale the tallest of trees, should you? What example are you setting for your teammates? And what happens when you have that one little misstep? The risk is not worth it – to you or the rest of the organization.
Numerous resources can help you set up a safety-first culture:
- Management must prioritize health and safety of their workers
- Squash any negativity toward safety
- Take preventive safety measures – including utilizing computerize maintenance management software (CMMS)
- Find and encourage “anchor points of safety” – the leaders who actively promote these good habits and make a positive example of these leaders
- Include safety as a core tenant in your new employee onboarding as well as continuing education
- Celebrate safety awards
Software can be a great help in safety initiatives. Documentation is critical to many processes. Step-by-step procedures show us how to do a standard preventive maintenance task on an asset/facility. Why not the same for safety? Having direct access to safety-related procedures such as lock-out/tag-out, job safety analysis (JSA) procedures and safety data sheets can be very helpful.
Below are a few examples of how Brightly Asset Essentials CMMS helps to automate safety initiatives:
Safety Programs
“Safety Programs” can be anything from disaster planning, plant/facility shutdown, fire drills, (personal protective equipment (PPE) training, weather-planning, lock-out/tag-out, safety data sheets, etc. This readily-available documentation is essential to positively affect our organizations. Asset Essentials allows you to track every safety program, including detailed descriptions, who is responsible, review dates, associated documents and more.
Below is an example of safety programs within Asset Essentials.
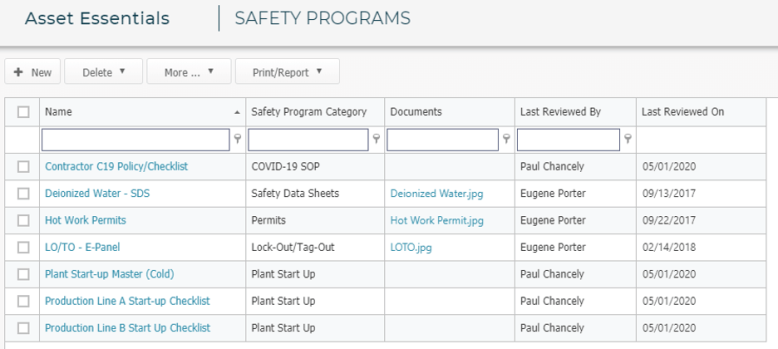
Every safety program in Asset Essentials can be associated with individual work orders – both preventive and corrective. For example, let’s use a PM (preventive maintenance) that requires you to be on a ladder and changing a fluid that has some level of safety risk. Not only will the Asset Essentials PM have step-by-step procedures for the actual PM, but also easy access to the ladder-harness instructions/video as well as that fluid safety data-sheet - all right from your computer or mobile device. This is safety automation at your fingertips. It is critical you make this as easy as possible for your teams to have access to this safety information.
Make Sure Your Team is Trained
Asset Essentials allows you to track all team members, including what training/certifications they have taken. You can have detailed descriptions of the trainings as well as a record of when any certification expires so you can ensure recertification compliance.
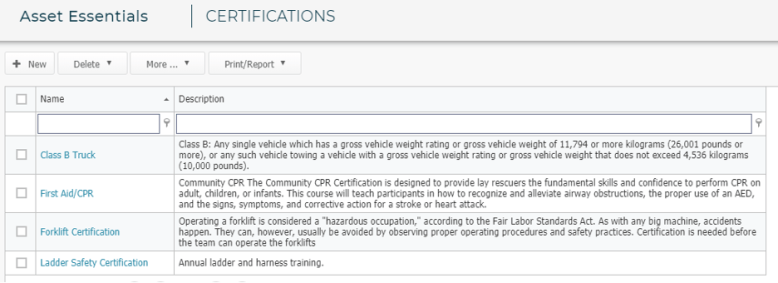

Track All Incidents Inside Asset Essentials
OSHA requires incidents in the workplace to be tracked and reported. Asset Essentials allows you to log every incident from near-miss to actual injury events. In the US, organizations are required to post the “OSHA 300 log” – Asset Essentials can print a generic one with all reported incidents. Note, these forms are by state, so ensure the Asset Essentials version is acceptable.
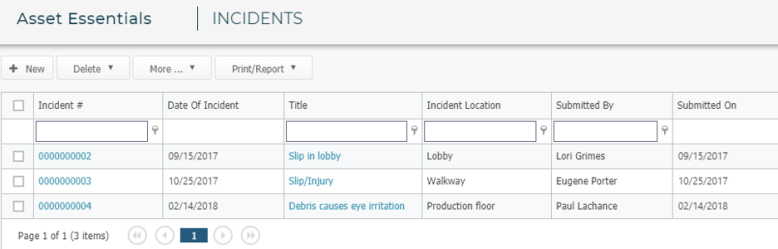
Better Maintenance = Safer Workplace
Even if you take formal safety initiatives out of the equation: better running facilities, buildings, factories, assets, etc. through solid preventive and predictive maintenance will create a safer work environment. When things break, they become less safe – for everyone involved.
Asset Essentials allows you to setup and schedule detailed preventive maintenance procedures. This could be to automate a safety inspection as well as the actual maintenance procedure. Setting up solid preventive maintenance allows for operational experts to spot and correct minor problems before they become major and thus more likely to create an incident with staff. These PMs can also indicate what safety equipment needs to be used as well as direct access to the documentation (steps, documents, videos, etc.).

Report Your Progress
Between tracking incidents and safety-related work orders in Asset Essentials, you can get a good idea of how your safety initiatives are working overtime. It is helpful to set up a safety key performance indicator (KPI) to track this progress. Place this right on the dashboard in Asset Essentials so that the team can see the progress – critical in a safety-first culture.

Conclusion
Given my length (numerous decades) in the operations field, I am happy to see progress on safety. I clearly recall previous generations joking about safety – the safety team, the procedures, etc. Fortunately, this has changed. We still have work to do – the culture and efficiency of our organizations demand this. The tight margins, escalating costs and related headwinds in today’s operations environment also demand we be as cost-effective as possible. A safety-first culture is good for us and our organization’s bottom line.
-----------------------------------------------
Sources:
- https://www.bls.gov/iif/
- https://www.bls.gov/opub/btn/volume-9/nearly-50-years-of-occupational-safety-and-health-data.htm
- https://www.osha.gov/data/commonstats#:~:text=Worker%20deaths%20in%20America%20are,2.8%20per%20100%20in%202019
- https://www.osha.gov/penalties
- https://injuryfacts.nsc.org/all-injuries/costs/societal-costs/
- https://www.supplychainbrain.com/blogs/1-think-tank/post/32165-safety-culture-in-the-supply-chain-getting-back-to-basics