Capital Planning in Manufacturing: How to Build a Blueprint for Long-Term Growth
In manufacturing, capital planning is an integral part of building long-term growth, ensuring that your investments in production assets and infrastructure not only increase productivity, but also create a sustainable future for your business.
Without proper capital planning, manufacturers risk unplanned downtime, unpredictable costs, and missed opportunities to optimize operations. A structured approach to capital planning helps manufacturers assess, prioritize, and manage their investments more effectively, paving the way for a sustainable future and continued success.
Below, we’ll review the capital planning process in further detail.
Why capital planning matters
Capital planning focuses on enhancing productivity and profitability through long-term investments in equipment, facilities, and technologies. It’s not just about finding areas to allocate your funds—it’s about making informed decisions that will deliver sustainable returns over time.
A well-informed capital plan can reduce your financial risk, increase operational efficiency, prevent unexpected asset repairs through proactive maintenance, and support overall business growth.
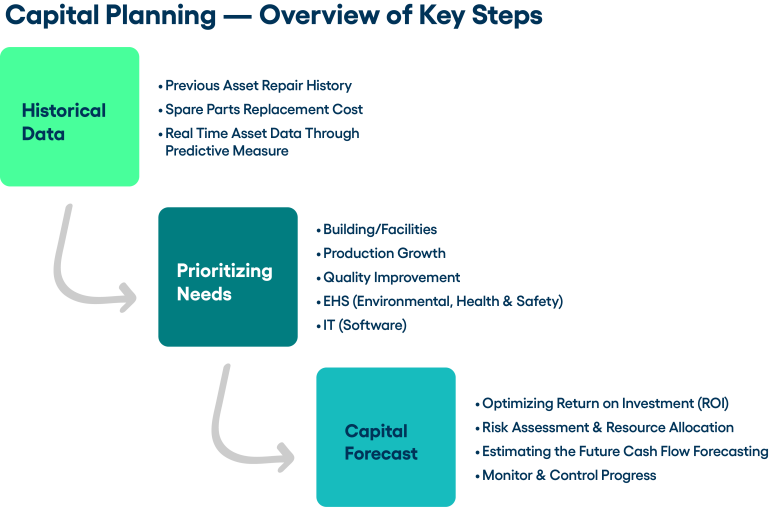
Best practices for successful capital planning
To maximize the success of capital planning efforts, manufacturers should follow these best practices:
- Align plans with business strategy: Ensure that all capital projects support the company’s broader strategic goals, driving improvements in productivity, efficiency, or sustainability.
- Communicate and collaborate: Keep all internal and external stakeholders informed throughout the project lifecycle. This includes production teams, finance, quality control, and third-party contractors.
- Plan for contingencies: Always have a backup plan. Whether it’s ensuring you have multiple suppliers or allocating extra capital for unexpected costs, contingency planning helps keep projects on track.
By following these best practices, you can ensure your capital planning processes support business growth, reduce risks, and optimize your returns.
Leveraging real-time and historical data
To build a solid capital plan, manufacturers must rely on both historical data and real-time insights to inform their decisions.
- Historical data: By analyzing previous trends, manufacturers can make more informed decisions about where to invest. Understanding past repair histories and spare parts costs helps companies prioritize needs, create more accurate budgets, and allocate funds more effectively.
- Real-time asset data: Predictive technologies provide manufacturers with valuable insights into asset performance, helping them detect abnormalities or patterns in asset failures before they become a major problem. Monitoring real-time trends and asset conditions allows manufacturers to create a proactive plan, reducing unexpected breakdowns and optimizing productivity.
By combining historical data with predictive analytics, manufacturers can make smarter decisions that drive growth and ensure long-term operational success.
Prioritizing investment needs
When it comes to capital planning, manufacturers should prioritize investments based on their most critical needs. Some key areas to consider are:
- Building and facilities: Investing in infrastructure, such as HVAC systems, boilers, or air compressors can enhance operational efficiency while reducing energy costs.
- Production growth: Installing advanced production lines or upgrading equipment can increase throughput and improve overall product quality.
- Quality improvement: Purchasing new equipment or other testing tools can ensure consistent product quality with fewer errors.
- Environmental, health, and safety (EHS): Upgrading safety systems or environmental controls can help manufacturers stay compliant with regulations while creating a safer workplace.
- Technology: Investing in software upgrades, such as ERP or CMMS systems, can keep manufacturers competitive and ensure smoother operational workflows.
5 ways to manage risk in capital planning
Risk management is a critical component of capital planning. By identifying, analyzing, and mitigating risks, manufacturers can protect their investments and ensure project success. Here’s how to effectively manage risk:
- Identify potential risks early: Understand the risks your company faces, whether it’s inflation, regulatory changes, supply chain disruptions, or environmental factors, and factor them into your decision-making.
- Analyze the impact of potential risks: Evaluate how likely these risks are to occur and understand what impact they would have on the business.
- Prioritize risks: Focus on the risks that have the highest potential to disrupt operations or increase costs.
- Manage risks: Create actionable plans to reduce or eliminate risks, delegating responsibilities to key team members of your team to ensure tasks are completed.
- Track risks: Maintain ongoing communication with stakeholders and monitor mitigation efforts to keep projects on track.
Proactively managing risks can help manufacturers avoid costly setbacks and maintain control over their capital planning initiatives.
Conclusion
Capital planning is a vital process that supports both long-term investments and short-term successes in manufacturing. By carefully assessing investment needs, calculating ROI, managing risks, and following industry best practices, manufacturers can enhance productivity, improve employee satisfaction, and maintain a competitive edge in the market. Ultimately, a well-executed capital plan can help you drive sustainable growth and secure the future of your business.
As important as it is, capital planning is just one part of what a complete asset management solution provides. If you want to learn more about how you can use your operational data to improve capital planning and manage your assets (so they don’t manage you), check out my recent webinar.
Or click here to see how other manufacturers are using an asset management solution to simplify their investments.