Preparedness in Energy Management: Part 2
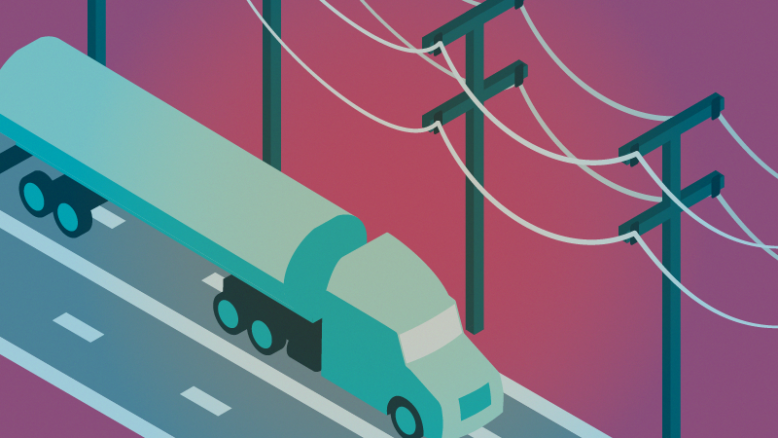
This is the second part of our “Preparedness in Energy Management” blog series overviewing the three critical pillars of strategic energy management.
- People: Who is managing energy?
- Processes: How is energy managed?
- Technology: What do we manage energy with?
In this blog, we will highlight the importance of great, sustainable processes as it relates to managing energy.
Did you miss Part 1: People? Check that out here!
Part 2 - Process
“Trust the process.”
“You can’t manage what you don’t measure.”
“What gets measured gets improved.”
A quick internet search will provide thousands of quotes about the importance of a good process. Why? Because, simply, it’s important.
No one would argue the fact that the smoothest manufacturers, the best sports teams, the most efficient organizations all have tested, sustainable processes. We all know that consistency yields results and in Part 2 of our blog series, we’ll explain what a consistent energy management process looks like.
Starting with a good process
To start, it’s important to acknowledge that there’s no need to totally recreate the wheel here. There are countless guides to energy management processes out there, and some are really good! The goal when looking at processes is looking through the lens of preparedness. And let’s be honest, arguably the most important part of being prepared for anything is having a plan.
Enter the APPEM (pronounced app-em) model. Why do we love this continuous improvement model? Aside from the fact that it can be used for virtually any process, it is also scalable.
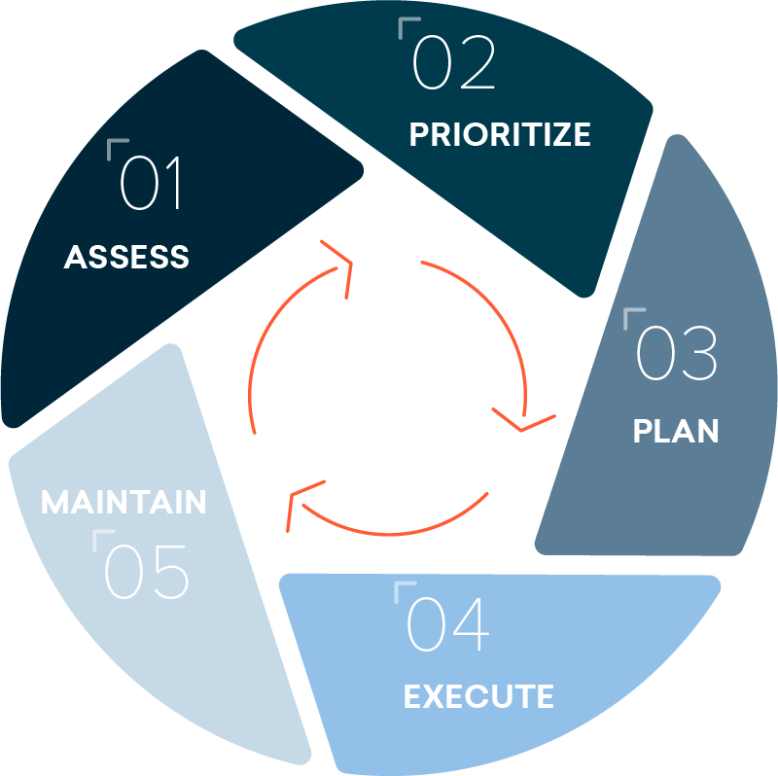
- Just getting started in energy management for a small organization with a few local facilities? APPEM.
- Do you manage a multi-site, international portfolio of buildings with a team of energy engineers? APPEM.
- Are you somewhere in between? You guessed it… APPEM.
So, let’s break it down. APPEM stands for:
- Assess
- Prioritize
- Plan
- Execute
- Maintain
Assess
Remember the “manage what you measure” quotes? Well, that’s assessment. The snapshot in time. The measuring. The baseline. Following the “A” phase, you should be able to answer questions like:
- What are the raw facts of my organization’s utility consumption today?
- At what facility or site are we spending and/or using the most utility resources?
- What utility services cost our organization the most to use?
- What is normal?
As one of our clients recently stated, 'Because I track raw consumption and cost data over time, I’m able to easily say, "See that? That’s not normal."'
Unfortunately, we often see that this very vital step is only given a cursory glance, if at all. Why? Because it can admittedly take some time and, for best practice, requires investing in technology the organization might not have (something we’ll discuss in part 3). However, just like pouring a solid foundation for a facility is a must, the consistent tracking of utility data is what any realistic energy management plan must be built on.
What to track:
- Infrastructure (facilities/sites, accounts, and meters)
- Major utility services (electric, gas, water)
- Utility billing data (consumption, demand, cost, billing days, rates)
- Advanced meter data (15, 30, 60-minute interval data)
- KPI data (weather, occupancy, square foot/meter, production values, school days, etc.)
Action item : Simply put, start tracking data. In today’s world, we can’t credibly operate our organizations without it. Though we understand an Excel spreadsheet is often the most realistic starting place, we recommend investing in software designed for this purpose, like Brightly's Energy Manager.
Point of focus : Start with major/critical infrastructure first – think your biggest buildings or most heavily used/occupied buildings. Focus on the “what to track” items above for the most recent two years and onward.
Prioritize
You’ve just crushed your assessment. You know that your administration building/critical access hospital/city hall/plant site #4 is your heavy hitter. The two- to three-year trends show a sharp increase in utility usage per occupant, and it’s worse during harsh weather days. New Indoor Air Quality (IAQ) protocols are playing a large role in increased energy usage, but because you’ve been trending for multiple years, you know COVID isn’t the only culprit. You’ve got a mixture of good, bad, and ugly in terms of where your assets are in their lifecycles. Finally, you recognize that occupant comfort complaints have been steadily increasing.
So, where do you start?
First and foremost, what are your goals?
Having goals is important for a number of reasons, and in the scenario above, they are what will keep you “on the road and between the lines.” In healthcare, for example, your goals may prioritize occupant comfort. So first, you’re going to more deeply explore the comfort complaints and understand where you may have temperature or humidity issues.
Or, your goals may prioritize carbon reduction and you might consider increasing the size of your renewable portfolio or green purchased energy from the utility.
As a final example, you may have a simple, strategic goal that prioritizes pure use reduction year-over-year (YOY). You might combine some operational changes, like control set-point and schedule changes, with capital improvements like new insulation or HVAC upgrades.
Bottom line is to align on your organizational goals and look to those goals to help you prioritize what to do and in what order.
Action item : Work to establish (or revisit) your organization’s energy, conservation and/or sustainability goals. Things like: 5% use reduction YOY, carbon reduction of 50% by 2030, compliance to certain challenges/initiatives etc.
Point of focus : Make simple, achievable goals for year one – goals that your organization will hit barring complete disregard for conservation. So much of energy management requires buy-in and commitment from building occupants and stakeholders. Achieving early wins for the organization (and celebrating them) is one of the best ways to build long-term momentum.
Recommendation : Need help? This is a great time to leverage industry expertise and engage with an engineering or auditing firm to conduct energy audits of your buildings. Learn more about how to conduct energy audits here.
Plan/Execute
Arguably the simplest step conceptually, the planning and execution phase puts action to your energy management strategy. You’re implementing stakeholder communication methods, coordinating contractors and project timelines, and ensuring occupant comfort is maintained and interruption is minimized.
A few tips for this phase:
- Don’t neglect low-hanging fruit in sole favor of large, eye-grabbing capital projects. Planning for, and executing on, things like consistent preventive maintenance schedules are some of the best energy conservation measures (ECMs) you can implement.
- Prepare for measurement and verification of the project. If applicable, did you include sub-metering infrastructure during the retrofit planning? Have you collected (and have a process for continual collection of) billing data in order to report on impact? Often, the post-measurement of a project is neglected, or delegated to the contractor at best. As we’ll discuss next, this can reduce your momentum.
Action item : Review or create checklists and walkthrough procedures in order to continually find low-hanging fruit opportunities. Ensure planned maintenance activities are scheduled and documented, as well.
Point of focus : Ensure your organization (or the contracted organization) has an industry standard, third-party process for measurement and verification documented and prepared before project completion.
Maintain
Lastly, what we mean by “maintain” in the context of this blog is measure and communicate results. Keep in mind, in this phase you aren’t communicating expectations, you are communicating results.
Did the project actually meet guaranteed savings? Did the savings from that project overperform?! Whatever the outcome, we recommend getting help (or further educating yourself) on calculating and reporting to stakeholders.
This is an exciting and meaningful phase, and studies show that people want to work for sustainable organizations that solve problems and achieve goals. Increased communication surrounding your plan lets them know they do.
This could look like: "This solar project will cost X, we are getting grant funding in the amount of Y,’ and our ROI will be Z. This will move us 25% closer to our carbon reduction goal.”
Action item : Establish a regular follow-up cadence on the results of the organization’s energy strategy. This might quarterly, biannually or annually.
Point of focus : Communicate in terms that resonate with your audience. In this case, you are communicating results, i.e., “Here is where we stand towards our goals. Here is how effective that project was, etc.” To put in language for an executive board or team: “Red bar is where we were. Blue bar is where this project has taken us.” To building occupants: “The savings from this project helped us create the equivalent of 10 FTEs.”
Planning + preparation = Great processes
Prepared energy management is procedural energy management. Have a plan, work the plan, recycle and repeat. Yet, as we’ve learned, it’s not all scientific – there is an art to energy management, namely in how we communicate to our building occupants and stakeholders.
The process of good, prepared energy management is both a science and an art.