Scrap & Rework: How CMMS Can Help Improve
Scrap and rework can be a profit killer. The costs of poor quality production are high and disruptive to operations. There are several methods employed by forward-thinking manufacturers to control/reduce scrap and rework – but the overall mission is to improve end-to-end quality, reducing inefficiencies, improving process and overall communication.
Computerized maintenance management systems (CMMS) can be a key part of your initiative to reduce scrap and rework, as well-maintained assets have better uptime, last longer and produce better quality parts and products.
What is scrap and rework?
Scrap and rework has numerous meanings, but at a high level:
- Scrap is the leftover/unused materials in the production process – the physical properties (or performance) of the product are out of design specification. This could be anything from metal shavings all the way to unused parts. Often scrap can be reused (at a cost).
- Rework is classified as parts created that do not pass quality inspections (defective, non-conforming, failed, etc.). The product's physical characteristics can be brought within specification by additional processing.
- Waste is different than scrap as it has no value except possible recycling.
Reducing scrap will have major benefits, including:
- Improved quality of finished produced parts, products and goods
- Helping production stay on schedule
- Reduced amount of rework
- Decreased line stoppages due to fewer missing parts
- Overall reduction of costs and improved profitability
- Reduced environmental footprint due to less waste
OEE (overall equipment effectiveness) formula uses good pieces in the quality portion of the formula. If you have too much scrap, your OEE is directly affected and conversely, when you clean up your scrap, you get a better OEE score.
Scrap is also considered one of the six big losses, an industry phrase for the most common causes of equipment-based productivity loss in manufacturing. In all events, scrap and possible subsequent rework will hurt manufacturing productivity, raise costs and negatively affect productivity.
What are the causes of scrap & rework?
There are many causes of scrap and rework, but the main buckets are:
- Machine malfunction
- Human error
- Poor quality materials
- Improperly communicated design changes
- Unimplemented design changes
- Miscalibration of assets
- Installing incorrect parts
- Lack of a quality assurance program
- Improperly maintained assets and productions lines
As a wise person said: “If you can’t measure it, you can’t improve it.” In the case of scrap and rework, you need to make a commitment to measure all sources of this issue – for example: by the hour, shift, part, material, operator, etc. By building analysis showing your scrap and rework bad actors, you can take proactive steps to remedy and reduce.
What are the solutions?
Numerous departments can help reduce scrap and rework. Operators (sometimes maintenance) need to do proper machine setup. This includes proper production readiness, perform pre-operations checks/inspections and/or perform quality control checks.
Other areas that can help prevent scrap and rework include:
- Calibrations – not only setting things like tolerances but also checking material delivery drops or output, temperature control, torque specs, etc.
- Tooling – for example, cutters need to be sharp or forming equipment needs to be able to hold a profile
- Aesthetics– things like color, finish, packaging, more typical of a quality assurance inspection, can also be related to a machine’s set-up
Operators are in an excellent position to catch problems early to reduce scrap and rework, especially aided with best practices such as total productive maintenance partnered with software such as CMMS (computerized maintenance management system).
Learn about 4 methodologies to help you avoid maintenance profit killers.
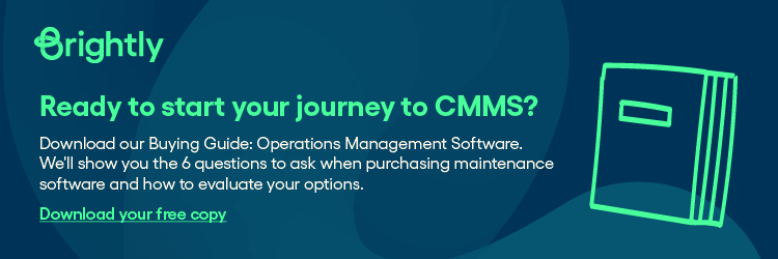
How CMMS helps
CMMS is an integral part of ensuring that your assets are running at their peak abilities.
CMMS not only reduces downtime and stretches the life of an asset, but a properly maintained asset will produce better quality parts and products.
Preventive maintenance (PM) is a key function of the maintenance organization within a manufacturer. The Society of Manufacturing Professionals (SMRP.org) call for a 80% preventive/20% corrective work order ration to be considered “stable” with a 90/10 ratio considered “world-class.” Many are not at that level, but if you are, you likely have very low scrap and rework. Wherever you are, having a key performance indicator (KPI) will show you if within your preventive/corrective work order goals.
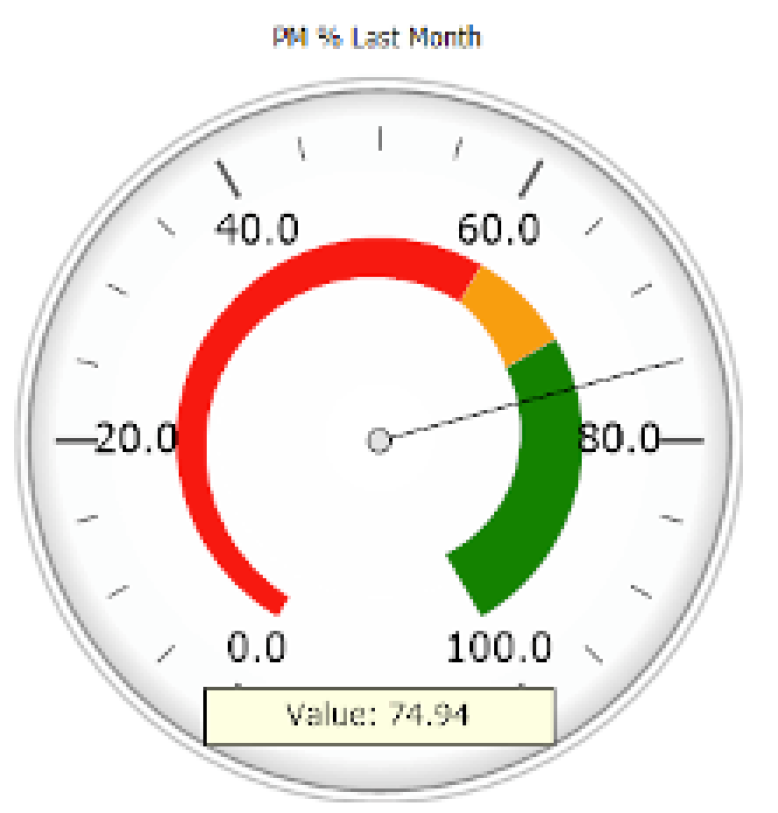
Using CMMS will:
- Automate your PMs
- Make sure you have the right people, tools and parts for the job
- Use Industry 4.0 technology such as IIoT to turbocharge
This can extend beyond the maintenance team to the actual operators (as discussed in the TPM section). These key front-line workers can have simple instructions for basic maintenance and cleaning, as well as add in meter readings (numerical readings from assets that can perform early detection of issues). Below is a simple example of an operator pre-shift task (PM) – essential to catching scrap and rework problems as early as possible.

CMMS can also provide excellent analytics, reporting and key performance indicators (KPIs) to help identify bad actors that would be contributing to scrap and rework.

Conclusion
In this hyper-competitive manufacturing world, we need to be efficient, smart and productive everywhere we can. Reducing scrap and rework is one of these areas where direct improvements can be made.
The combination of best practices and CMMS technology will not only help reduce scrap and rework but have other general benefits to the organization, controlling costs and ultimately improving profitability.