The 6 Steps to Plastic Injection Molding
Injection molding gives manufacturers the freedom to create all of their products over and over again with just one mold. This is one of the biggest industries inside of plastic manufacturing, with an estimated market size valued over $280 billion in 2016. With an industry this large, sustainability is a key factor. Not only sustainability for the plastics but for the machines that are running throughout the day. First, it is important to know how plastic injection works before diving into what needs to be fixed and what innovation is happening.
Injection molding is done in a 6-step process.
- The first step of injection molding is the process of clamping. The clamping unit is what pieces together the mold before the injection takes place. The two sides of the mold are placed into the unit and then the machine pushes the two halves together to prepare for the next step: injection.
- Once the clamping phase is complete and the two halves are put together, the injection of the plastic begins. The plastic, usually in the form of pellets, are then pumped into a container in which they are melted down to a complete liquid. This liquid is then injected into the mold, maintaining temperature throughout the process.
- Next comes the dwelling phase, in which the plastic is filled to the entirety of the mold. This is done through pressure. Pressure is applied to the mold so that way the plastic covers all of the mold cavities to ensure the product will come out correct.
- The fourth step is the cooling stage and is the most straightforward. The mold is left alone so the plastic inside can cool and start to form as a solid inside of the mold.
- Next step is the mold opening.
- This is followed by the final step of ejection, which reveals the final plastic product from the mold.
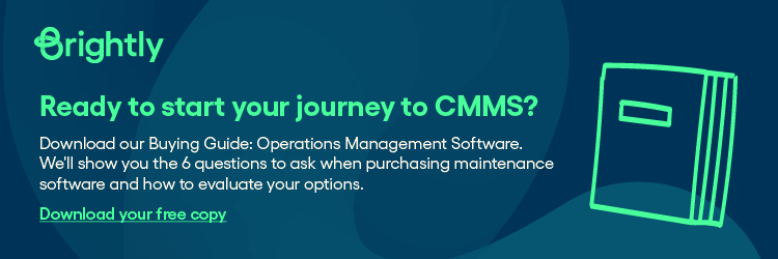
Now that we know how plastic injection occurs, let’s focus on how sustainability plays a huge role.
Plastic is one of the cheapest materials to produce and it’s used by a large variety of companies and people, making it of great demand. With this high demand, it’s vital that manufacturers focus on new advancements in technology that allow machines to run longer and more efficiently, conserving energy and producing more, faster.
One key way to achieve asset longevity and maintain a sustainable environment is to use a CMMS to track key performance indicators around energy consumption and failure rates. A CMMS can ensure that manufacturers reap the benefits of predictive maintenance to make sure machines are running smoothly and address issues before they happen. Tracking energy usage can be vital in both determining issues with any equipment, as well as ensuring energy consumption is at a minimum. It isn’t just the machines that need to be sustainable; it’s important for the plastic resources, as well.
Environmental concerns are a key focus for the plastic industry. This concern goes far and beyond just equipment energy usage, but also the amount of plastic scrap produced. Both go hand in hand, as equipment that is maintained better produces at its expected quality and limits scrap plastic, as well. Strategies like using energy efficient machines and recycling scrap plastic are both efforts going into making everything more sustainable. In addition to limiting scrap plastic, many manufacturers are using an alternative to normal plastic, such as bioplastics, which are biodegradable over shorter amount of time when compared to normal traditional plastics.
Practices like these combined with a system for tracking maintenance and assets is a match that cannot be beat when it comes to saving money, machines and the environment.