Simplifying Lockout/Tagout Procedures With A CMMS
For companies that work with large machinery, it's vital to control hazardous energy that machines can emit. The Occupational Health and Safety Administration (OSHA) requires that certain safeguards are in place for employees to prevent injuries or death. Hazardous energy control is one common way for organizations to stay compliant with those regulations for keeping employees safe.
OSHA's accepted standards are lockout/tagout procedures, a step-by-step way to ensure machines in need of maintenance or service are safe to work on.
What is lockout/tagout?
Lockout/Tagout (LOTO) refers to practices and procedures that safeguard employees from the unexpected energization or startup of machinery and equipment. Specifically, unexpected startup of machinery during service or maintenance can release energy that can be toxic or otherwise hazardous to the people working around them.
LOTO safety is a key strategy in Occupational Health and Safety Administration (OSHA) compliance standards that organizations must meet and maintain. Following LOTO procedures is vital in maintaining a safe, properly functioning workplace, and helps ensure the health and safety of maintenance employees.
Why is lockout/tagout important?
Machines that operate through electrical, mechanical, hydraulic, pneumatic, chemical, and thermal methods often emit hazardous energy that can be a danger to those who work around or on them. Employees who service or maintain machines and equipment are at particular risk of exposure to this energy since performing service or maintenance on them often results in the release of stored energy. This can result in injury or even death to workers without the proper precautions. Craft workers, machine operators, and laborers are among the groups at the highest risk.
Controlling hazardous energy (lockout/tagout) is one of OSHA’s top 10 most frequently cited standards. It’s essential for companies that work with these machines to ensure they’re operating safely, with minimal risk to those who work on and around that equipment during servicing and maintenance tasks.
What are the steps of lockout/tagout?
Lockout/Tagout procedures are designed to ensure the safety of workers when they are working on or around equipment that has the potential to release stored energy. The process of Lockout/Tagout involves several important steps to ensure the safety of affected employees, and often are managed through a computerized maintenance management system (CMMS).
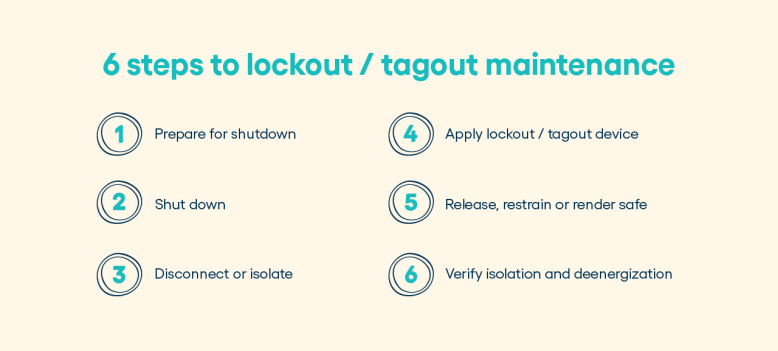
1. Prepare
Before starting any Lockout/Tagout procedures, it is essential to have a plan in place that includes identifying hazardous energy sources and determining which devices need to be locked out or tagged out. The preparation step should also include selecting appropriate lockout devices and tagout devices and ensuring that all employees involved in the process are appropriately notified that equipment will be shut down and trained in the Lockout/Tagout procedures.
2. Shut down
Once the preparation step is completed, the next step is to shut down the equipment or machinery to be serviced. This involves following the manufacturer's instructions or standard procedures to ensure a safe and efficient shutdown per normal operating procedures.
3. Isolate
After the equipment or machinery has been shut down, the energy source(s) must be isolated. This means disconnecting or isolating the energy source(s) from the equipment to prevent an accidental release of stored energy using an energy-isolating device, such as
- Valves
- Breakers
- Switches
- Blank flanges for piping systems
- Restraining devices
4. Lockout/tagout
Once the energy source has been isolated, apply the lockout or tagout devices. This involves physically locking and/or tagging out the energy source(s) using appropriate devices that prevent the equipment from being turned on or activated, keeping them in a “safe” position.
5. Check stored energy
After the energy source(s) have been isolated and locked or tagged out, it is essential to verify that there is no residual energy left in the equipment. This may involve releasing any residual pressure or discharging any stored capacitors. For example, closing a valve on pneumatic- or hydraulic-powered systems isolates the system from its primary energy source. Any air or liquid remaining in the system may be dangerous, so bleeding liquid or venting the air helps ensure there are no accidental exposures and injuries.
6. Verify
The final step of Lockout/Tagout procedures is to verify that the equipment is fully de-energized and that all Lockout/Tagout procedures have been properly implemented. This may involve visually inspecting the equipment, testing the controls or switches, and verifying that all affected employees are aware of the Lockout/Tagout procedures in place. This last step is crucial to ensuring employee safety, verifying that the machine or equipment is disconnected from its energy source before maintenance begins.
Lockout/Tagout procedures are essential for preventing workplace accidents and injuries caused by the unexpected release of stored energy. By following these Lockout/Tagout steps, employees can work safely on or around equipment or machinery that has the potential to release stored energy.
Simplifying lockout/tagout with your CMMS
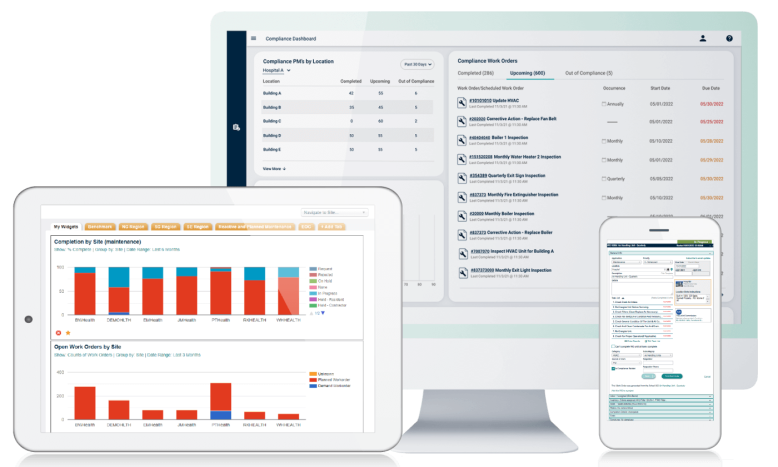
Using a computerized maintenance management system (CMMS) can simplify and automate Lockout/Tagout procedures, making the LOTO process easier and safer. By reducing the manual efforts needed to provide the proper safety parameters for employees, a CMMS can reduce the potential for human error, and offer safeguards that will keep employees safe while working on equipment.
Storing critical LOTO information: A CMMS stores all of the critical information related to LOTO procedures in one centralized location. This includes information about energy isolation, isolation devices, and other important details. By having all of this information in one place, it becomes easier to ensure nothing is missed, and all steps are being taken to properly implement LOTO processes.
Including LOTO instructions on work orders: A CMMS has the capability to list LOTO instructions on work orders for specific pieces of equipment, ensuring employees are aware of the LOTO procedures that must be followed before working on that particular piece of equipment. By integrating LOTO procedures into work orders, employees can quickly and easily access the information, using it as a checklist to ensure compliance.
Providing compliance documentation: OSHA lockout/tagout regulations require that companies keep detailed records of LOTO procedures. A CMMS can provide documentation of those procedures, including the steps taken to isolate energy sources, apply LOTO devices, and verify that equipment is safe to work on. This documentation can be easily accessed and updated, ensuring companies remain compliant with OSHA regulations.
Automating LOTO processes: A CMMS can automate some of the LOTO processes, such as generating work orders and assigning tasks to employees. This can save time and reduce the risk of human error. For example, when a work order is generated, the CMMS can automatically include LOTO instructions for that particular piece of equipment.
Ensure maintenance safety with Brightly Software
Ensuring your Lockout/Tagout program is accurate is a critical safety measure for companies that work with equipment that works with potentially hazardous materials. Brightly’s CMMS helps create a safe work environment for your employees by tracking and automating critical maintenance information, like LOTO procedures. Speak with one of Brightly’s experts and learn how Brightly can help to simplify maintenance safety and compliance.