CMMS vs. ERP: Which is Better for Manufacturing Maintenance?
In any manufacturing industry, achieving productivity and efficiency targets is paramount. However, manufacturers are facing a wave of challenges like rapid automation, supply chain disruptions, artificial intelligence (AI) integration in various production processes, and most importantly, skilled labor shortages.
Choosing the right software to meet the demands of industry-wide maintenance management can be difficult. To address these challenges, manufacturers often turn to two primary systems: ERP (enterprise resource planning) and CMMS (computerized maintenance management systems).
Let’s break down both systems to clarify their distinct roles and how they can work together to improve maintenance and operations.
ERP: For end-to-end business management
ERP systems are designed to manage an organization’s entire business process end to end, including finance, human resources, sales, production, inventory control, warehousing, and supply chain management. ERPs serve as a centralized platform that integrates these functions, providing visibility to all stakeholders and enabling data sharing across the company.
However, companies with a more strategic approach and long-term vision may opt for a CMMS due to its in-depth asset management capabilities with reporting and analytics features that provide real time historical data to make informed decisions around capital planning, work order management, and asset lifecycles.
Some of the core benefits and outcomes of having ERP systems include:
- Streamlined supply chain management: Helps optimize raw material handling and ensure a smooth production process.
- Improved production efficiency: ERP enhances product quality, R&D, and development efforts.
- Better customer experience: Ensures delivery of finished products on time.
- Data-driven decision making: Provides stakeholders with real-time data for production planning, scheduling, and forecasting, based on existing client purchase orders.
CMMS: For asset performance and maintenance management
While ERP systems offer basic maintenance features, such as work order management and inventory tracking, they are more focused on managing the overall business.
CMMS, on the other hand, is laser-focused on managing and improving asset performance across an organization. It’s more user-friendly than ERP and offers advanced features like reporting, analytics, preventive maintenance planning, and MRO inventory management.
Many manufacturers today are shifting toward CMMS solutions because of their ability to provide in-depth insights into asset health, streamline maintenance workflows, and track KPIs like asset downtime, preventive maintenance (PM) compliance, and work order backlogs.
Some of the key benefits and outcomes of having a CMMS include:
- Enhanced asset efficiency: Track and optimize entire asset lifecycles.
- Extended asset lifespans: Proactively scheduling repairs to improve longevity.
- Minimized downtime: Eliminate unnecessary equipment failures with a proactive maintenance approach.
- Lower maintenance costs: Transition from reactive to preventive maintenance for cost savings.
- Visibility into labor and parts usage: Track labor hours and parts usage for each work order.
- Data-driven decision making: Use real-time data to support capital planning and asset management.
ERP vs. CMMS: A Quick Comparison
Even though ERP and CMMS focuses and serves different priorities across the organization they can still integrate to allow information sharing as well as to improve the overall productivity by making informed decisions in terms of overall financial planning, asset health portfolio monitoring.
The table below shows some basic comparisons between CMMS and ERP combabilities.
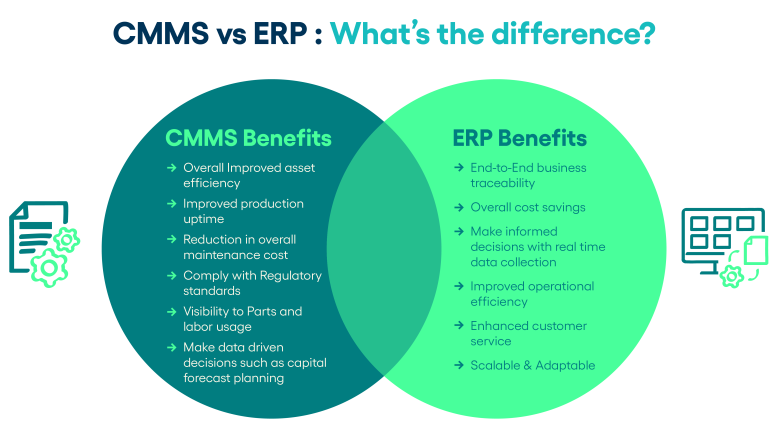
Why CMMS is the ideal choice for manufacturing maintenance
When it comes down to it, CMMS is the better option for manufacturing maintenance, for three key reasons:
It's more user-friendly
CMMS is designed to be intuitive for maintenance personnel. Technicians can log labor hours, track parts inventory in real-time, and even access data remotely via mobile devices—allowing them to complete tasks without unnecessary trips back to the workshop.
It streamlines maintenance workflows
CMMS offers a more efficient workflow for tracking asset lifecycle management, including repair history, spare parts costs, and BOM (Bill of Materials). By implementing a CMMS, manufacturers can shift from reactive to preventive and even predictive maintenance, relying on real-time data to inform decisions like asset replacement or capital planning.
It enhances data collection
CMMS acts as a single source of truth for all asset data, collecting essential information that can be integrated with advanced systems like IoT monitoring, predictive maintenance, and capital planning software. Asset data can also be used to perform root cause analysis (RCA) and failure mode and effects analysis (FMEA) to pinpoint the causes of equipment failure and justify asset replacement.
Take the next steps on your CMMS journey
If you’re ready to take control of your asset management with a CMMS, contact us today to discuss your specific needs and learn how a CMMS can transform your maintenance operations.
Or click here to discover more ways to level your work order management with a CMMS.