Digital Transformation is for Everyone
Digital transformation (DX) sounds technical, but at its core, it’s just about identifying real business challenges and opportunities with the help of technology. It’s a key part of the 4th Industrial Revolution, or Industry 4.0, that we’re living in right now, and it’s definitely not limited to big companies. All industries, from small to mega (especially manufacturing), can and should use a DX mindset to optimize operations, control costs, and stay competitive.
It’s Not Just About Technology
Despite what you might expect from the name, digital transformation is about a change in organization culture more than anything else. DX is a paradigm shift where you drop legacy technology-adverse attitudes (i.e., “we have always done it this way”) and look at business opportunities and challenges differently, always with an eye to where technology can help. For maintenance and related operations, this largely comes down to a more proactive mindset where you run “lean” and efficiently, largely with a predictive and ultimately prescriptive posture.
There is a legacy image of a maintenance worker that many manufacturers still think of: someone vital to your facility, but whom you never want to call in because it’d mean something has gone wrong. They can save your neck by fixing a critical asset when it breaks, but a break/fix mentality is expensive and disruptive, and you’ll wish you just paid better attention to the asset before unplanned downtime happened in the first place. Today we can do better, and once you have identified these challenges, you can find optimizations with new technology.
In the Industry 3.0 era (1960s-2010s), while we had advancements in electronics and computing power, it was often impossible to monitor and maintain every asset. Basic preventive maintenance on a calendar basis has been around for decades but can be inefficient and often not used. This resulted in a run-to-fail mentality in which maintenance workers only received information in person when they received a work order. With Industry 4.0, connectivity between people, facilities, and assets is essential and delivers a plethora of data critical to driving superior predictive maintenance operations. This allows for a more efficient team that can better maintain assets, have improved uptime, control costs, and create high-quality products. This is the heart of the value of DX.
Digital transformation really will benefit teams first and foremost. Many are worried that artificial intelligence and automation will replace humans in manufacturing — DX gets a bad rap for this. Like all previous industrial revolutions, technology will change how we work, cut costs, and increase productivity. This will allow our teams to work on more creative, value-producing, and strategic tasks. People will be learning new skills. This transformation has occurred in every industrial revolution.
Here’s The Technology Part
Digital transformation starts and ends with people and teams, but technology plays a vital role. With all identified challenges and opportunities, there will be a project involving modern tech. Some key examples:
- Computerized maintenance management system (CMMS): This is the backbone of maintenance organizations, managing assets and facilities, work orders, spare parts, and more. This is cloud-based and can be accessed anywhere, anytime on our computers and mobile devices. World-class software like Asset Essentials™ can save your team time, money, and your most important assets.
- Sensors for our assets and facilities (Internet of Things/IoT): A broad label to describe connecting all our facilities, vehicles, assets, and people, watching for small problems before they become large ones and feeding vital information into our CMMS. With Asset Essentials, work orders can be created the instant failure occurs, helping eliminate downtime.
- Digital twins: A digital twin is a simulation of a physical asset in a digital space. Allow for modeling, analytics, and testing for new features or hypothetical situations.
- AI/Machine learning: Both artificial intelligence (AI) and machine learning excel in finding patterns when people aren’t (or cannot be) looking. Generative AI like ChatGPT shows promise but is not currently at the front line of digital transformation for manufacturing. The best AI in manufacturing maintenance and related operations is harnessing the data, analyzing, and predicting failures well in advance of disruptive unplanned downtime.
Although these are all technology topics, ultimately these tools solve real-world business challenges. DX is never about just introducing technology, but using tech to help organizations be stronger, smarter, and more profitable. DX is about driving cultural and educational changes to use tech when appropriate.
How It Can Help
Digital transformation can be invaluable for improving productivity and defending against uncontrollable factors. In the few years, manufacturing and industrial organizations have seen record-high inflation, energy prices, a challenging supply chain, and rapidly changing workforce just to name a few challenges. We can’t control these macroeconomic issues, but we can operate lean/efficient and work around.
One example is looking at overall equipment effectiveness (OEE), a critical manufacturing metric that grades how efficiently our assets and production lines are running.
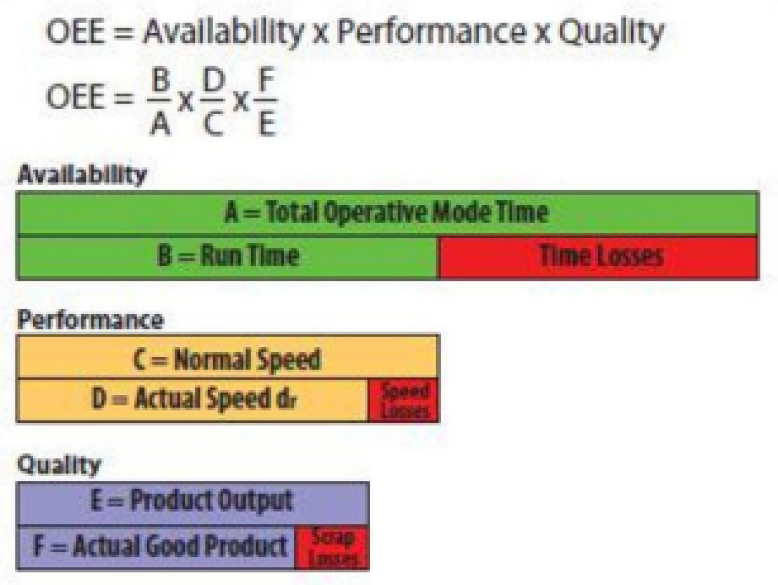
This is a combined measure of availability (uptime), performance (speed), and quality (percentage of viable products). Keeping all three of these numbers at the highest they can be is vital to maintaining a competitive operating environment. If your organization is suffering from poor OEE scores (or even worse, you cannot measure them), you likely have too much unplanned downtime and quality issues. These critical challenges can be solved with a DX mindset: Use technology to remedy the situation.
DX In Action: Smart Assets
If you are suffering from too much unplanned downtime, poor OEE, or similar, a DX initiative can really help. Brightly Smart Assets is an app interface that connects asset information for use in the workplace, and an example of IoT.
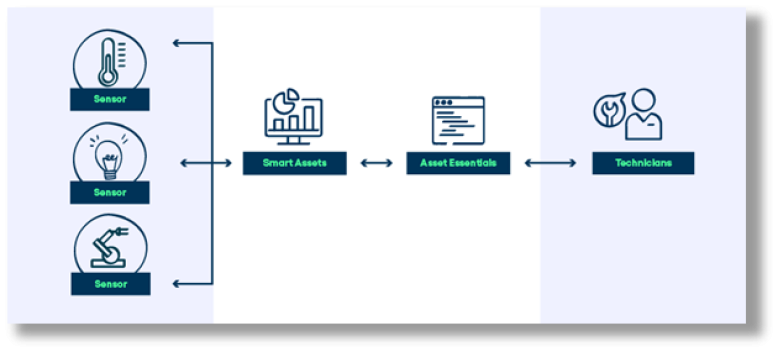
Raw data comes from sensors/assets attached to the assets including temperature, pressure, vibration, and many other measurements. This information is analyzed and when appropriate, generating a work order in Asset Essentials. From there, managers and technicians are alerted to potential problems immediately, allowing for immediate remedy while they are smaller and less disruptive. Team members cannot be watching our operations 24/7, especially given the challenges of hiring these days. Sensors can and will catch problems early, allowing people to apply their skills where they are most effective. This is a powerful example of the impact of DX.
DX Pays Off
Simply put, the return on investment of digital transformation is huge. There are needed investments to find operational improvements from DX initiatives, including training workers and implementing modern technology, but it will bring reduced long-term costs and significant improvements to productivity. When running on more proactive maintenance rather than a run-to-fail posture, you will save money and have a happier team. Asset downtime is a profit killer, slowing productivity, hurting sales orders, and requiring both higher CapEx and OpEx costs to fix. DX mindset and implementation of CMMS and IoT can really move the needle.
You Need a Good Partner - Brightly Can Help
Digital transformation sounds challenging and technical, but when broken down into simple parts, is very workable and can safely be integrated into your organization. Having a partner that can not only deliver the technology, but more importantly the education and partnership to implement with positive ROI is essential. Brightly and Siemens are at the forefront of DX, and our partnership will only continue to make us better.
Digital Transformation is 90% culture and education and 10% technology. Identify your business challenges and opportunities for growth. Break them down into identifiable projects, each of which will undoubtably utilize Industry 4.0 technology. Where technology can help, use it — today’s tools are more powerful than ever, easier to implement, and have a fast ROI. Ready to get started? Schedule a discovery call with a Brightly expert, scope your organization’s goals and challenges, and enjoy a custom demo to feel the world-class difference for yourself!