Operational Best Practices You May Not Know About: 5S
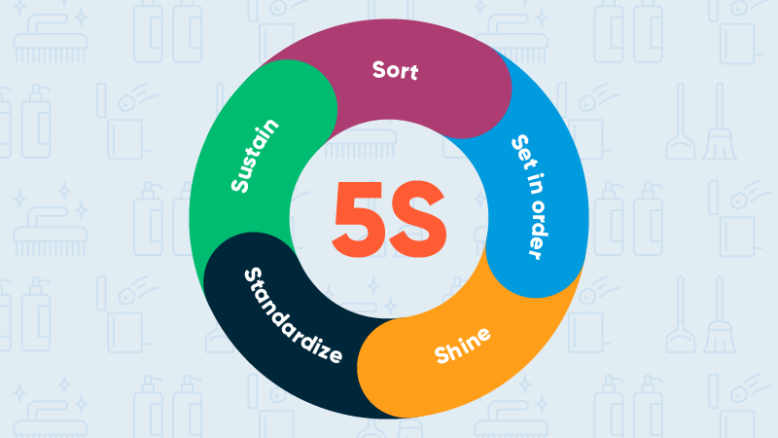
“Clean your room!” was a common phrase I heard growing up, especially as a teenager. Although I eventually broke the habit in my 20s, I now find myself uttering the same phrase to my teenage sons. My memory of my own response is foggy, but I am taking a highly educated guess that my son’s own response of “Why? I know exactly where everything is!” is similar to what I would have said. While it is true, my son might eventually find that missing phone charger I was looking for, and in the process locate several dirty dishes and might even notice that there is minor leak by his radiator – but none of this would be likely given the messy state of his room.
The great thing about 5S is it not only helps my high-school senior, but also huge organizations with lots of people, facilities and stuff. 5S is one of many best practices/methodologies that ensures operational excellence through a clean, organized and optimized environment.
Let’s explore more of what 5S is and how it can benefit your organization.
History of 5S
Although there has always likely been 5S-like “neat-freaks”, in the historical record, 5S traces its origins back to 16th century Venice shipbuilding. The original idea was to streamline production, which these early pioneers where able to do, building ships in days versus weeks. In post-war Japan and especially leading into the 1970s, the lineage of 5S appeared as part of the Toyota Production System. On a side note, this is Toyota Production System also included “Just-in-Time Inventory”, “Jidoka” and early origins of the “Visual Workplace” among other game-changing methodologies.
Originally, these disciplines/methodologies were a closely guarded secret at Toyota, but as the industry watched the rise of this manufacturer, many wanted to know their secret sauce. Now, 5S (and other TPS disciplines) are now widely adopted in manufacturing around the world.
What is 5S?
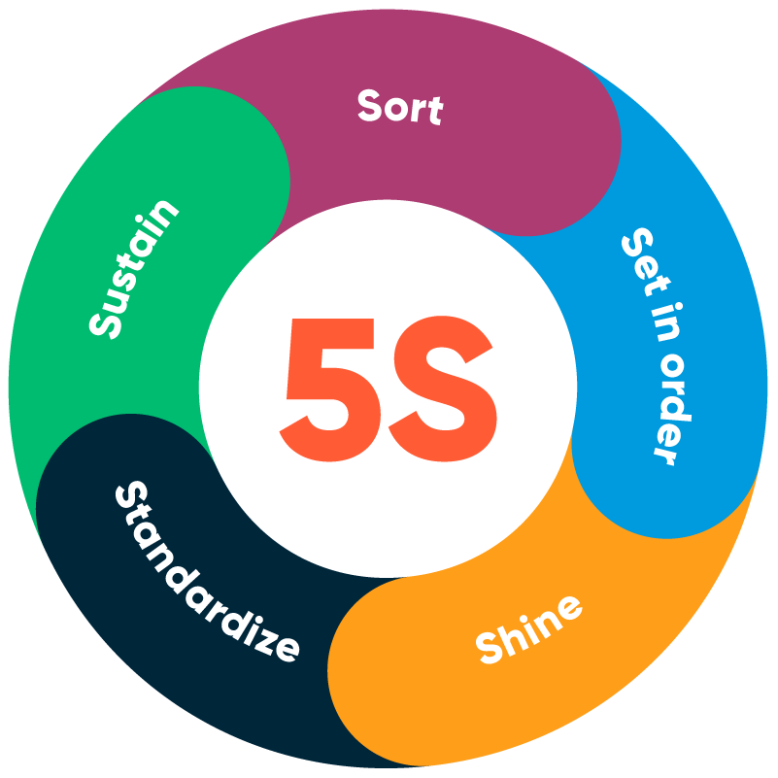
The 5S methodology is a systematic approach to workplace organization.
As you might have guessed, there are five major steps:
- Sort
- Set in Order
- Shine
- Standardize
- Sustain
At a high level, the steps of 5S involve going through items in a workspace, removing what is unnecessary, organizing items, cleaning, performing maintenance and making sure these things become habits.
Optimally, these steps should occur in this order and performed on a regular basis. At the end of a 5S implementation you will see characteristic things such as policy manuals, glow-in-the-dark tape or photoluminescent tape on the floor, colored bins, red tags, and 5S walks taking place. The ultimate goal is efficiency and promotes a lean operating environment.
When you see these “before and after” pictures, it is not hard to see how 5S makes everyone’s jobs much easier, more efficient and safer. Can you imagine trying to find a needed tool on the left? Or know if there is a maintenance issue that is creating a leak or other physical issue? Very difficult to tell. 5S will really makes for a better environment.
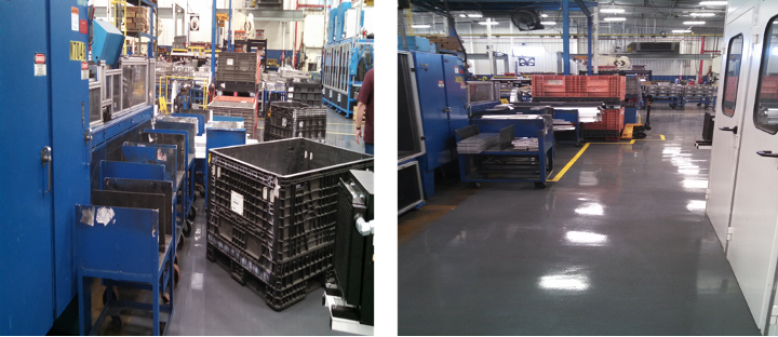
The steps of 5S
Let’s break down the 5S steps in more detail:
Sort (seiri 整理) – The process to sort/remove all unnecessary items from the location. If you don’t need it, don’t let it take space or create confusion.
Set in order (seiton 整頓) – The process of putting all necessary items in optimal place. You can see from the illustration how much better organized the space is. This not only includes physically placing everything in optimal order, but also marking these locations visually.
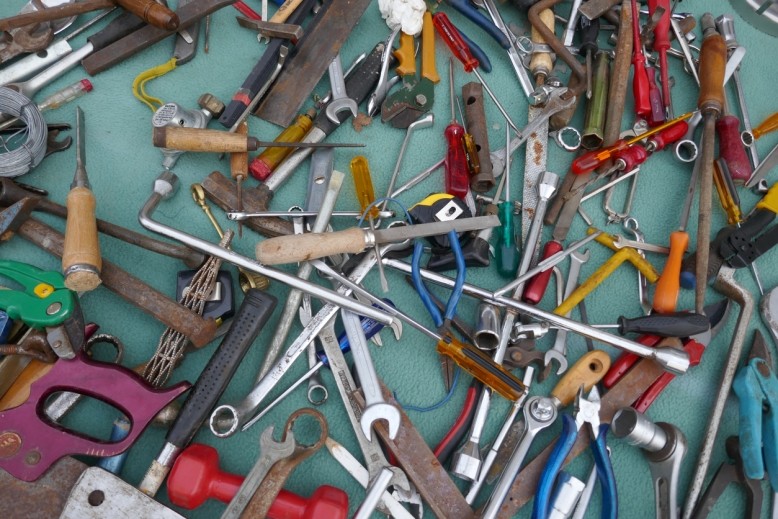
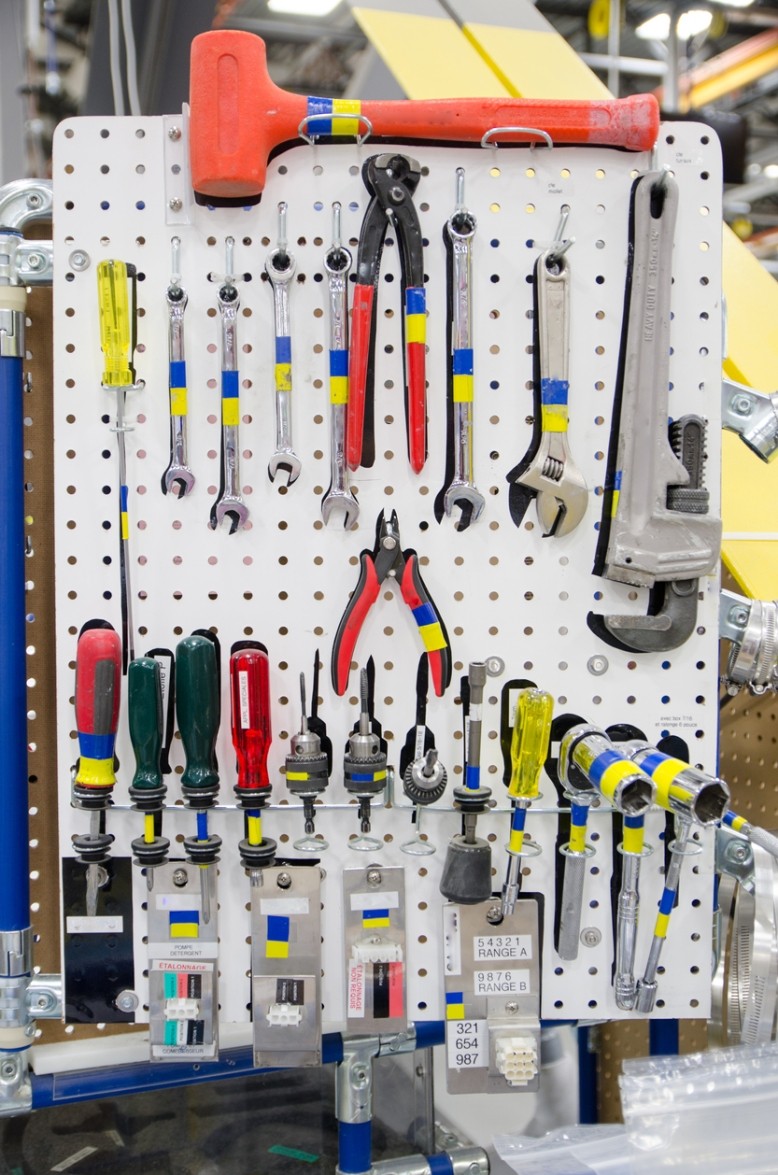
Shine (seiso清掃) –This process involves cleaning and inspecting the workplace, tools and machinery.
Standardize (seiketsu清潔) –This section standardizes the processes (sort, set, shine). Notice the documentation, guides and other helpful information to ensure that the 5S methodologies can be continuously managed.
Sustain/self-discipline (shitsuke しつけ) – This final area ensures that all 5S becomes a natural process. I’ve yet to hit this milestone with my teenage son, but ultimately, everyone on the team should "do without being told", maintaining 5S principles automatically.
Note: There is sometimes mentioned a “6th S” for “Safety”. Some organizations will implicitly note safety routines. I personally believe that safety is core to all of the “Ss”.
What are the costs of adopting 5S?
There are direct and indirect costs. An organization must take the time to make these improvements. This means stopping, debating (including using a “kaizen” if appropriate), and ultimately working thru the sort, set-in-order and shine phases. Also, the time needed to document and manage the process. There are also costs around cleaning, painting, putting down floor tape and other tasks within 5s.
What are the benefits of 5S?
Identifying specific numeric improvements might be difficult when adopting 5s principles. The entire, general “wellbeing” of the plant floor and teams running them will improve. 5s is clearly part of the lean manufacturing environment.
Benefits will include:
- Eliminate waste
- Higher quality, increased productivity
- Greater employee satisfaction
- A safer work environment
- Reduced costs and ultimately improve profitability
My kid will eventually (hopefully!) grow up and understand the importance and benefits of a well-maintained, clean and organized environments. The competitive nature of operations requires us to have these disciplines. Not to mention the financial, safety, morale and operation benefits!
Ready to get started with more efficient practices at your organization?