The 5s Methodology for Lean Manufacturing
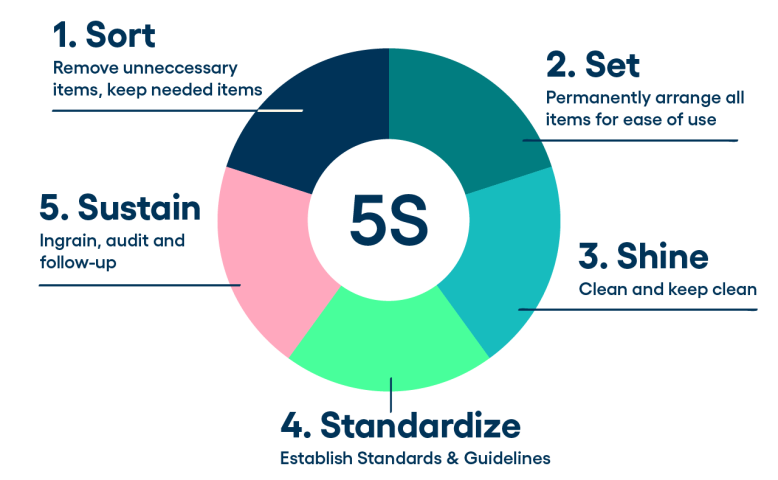
In lean manufacturing, 5s is a low-investment, high-impact manufacturing tool designed to massively enhance your daily operations.
It involves a simple, five-step methodology that, when followed, promotes better efficiency and higher levels of productivity by ensuring a safer, more organized, and more streamlined workspace.
The 5s Methodology
The steps of 5s in order are Sort, Set, Shine, Standardize, and Sustain.
1. Sort
In the Sort step, the goal is to minimize clutter and make it easier to locate the resources needed for work. This means all critical items, spare equipment, and parts inventory should be well organized, and all unnecessary items should be eliminated. Creating or utilizing a storage area near the workspace can make this easier by giving you a space to safely store spare materials and equipment.
2. Set in order
All items, equipment, and parts inventory should be given defined locations in the “Set” stage. Your objective here is to maximize accessibility, free up usable space, and prevent unexpected downtime by removing unnecessary obstacles.
Ensure all tools and equipment are labeled correctly so they are easily identifiable and stored in an easy-to-access location. And display visible signs in work areas where personal protective equipment (PPE) is needed and emergency equipment like fire extinguishers or hoses should be unobstructed and easily accessed if needed.
3: Shine
Ensuring all equipment, tools, and production areas are clean and sanitized is the basis for the “Shine” stage. This means cleaning all work areas, machines, parts, floors, walls, ceilings, storage areas, etc. PPEs should be sanitized and kept in good condition as well, so sanitation supplies should be safely stored and easy to access. It is also critical to implement a cleaning schedule for the production floor for more visibility and transparency.
4. Standardize
Each of the first three steps should be standardized and implemented across all departments during step 4. This allows all members of your organization to realize the benefits of your efforts and create a more unified, company-wide standard. Newly implemented operating and storage procedures should be consistently followed, environments should all meet regulatory compliance standards, and the results of your 5s audit should be posted and clearly visible for your team’s reference.
5. Sustain
Ensuring the 5s methodology is continuously implemented in your daily routines can help ensure your organization is maximizing its potential by removing any obstacles that could have a potential negative impact on productivity.
To ensure the 5s methodology is sustained, support senior leadership in having regular meetings to review effectiveness, give recognition to team members who actively adhere to the 5s initiatives, and allocate regular time and budget to highlight or improve 5s activities.