Asset Hierarchy Within Work Order Management Systems
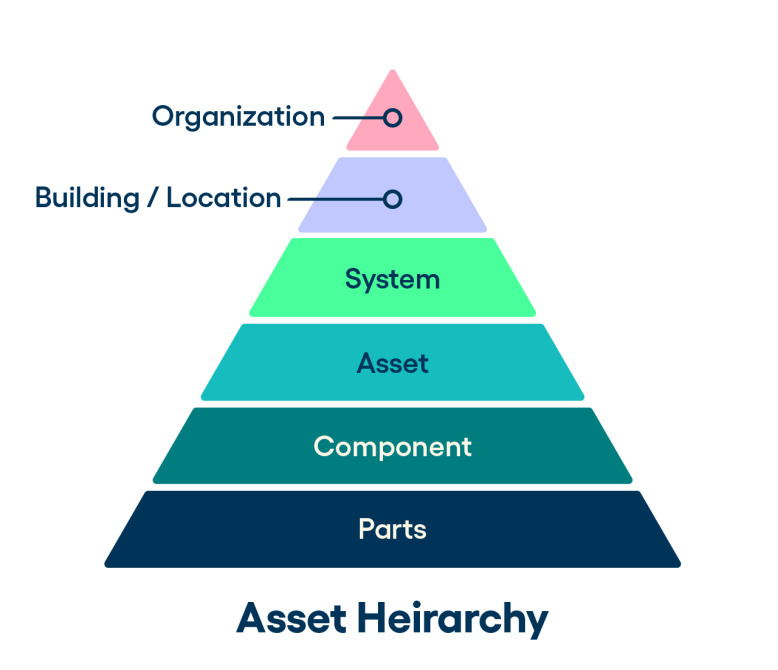
In today’s era of manufacturing, defining and establishing a well-structured asset management system is key to success. A key component of this is incorporating an asset hierarchy to effectively manage your day-to-day maintenance and operations.
What is an asset hierarchy?
An asset hierarchy organizes assets into different levels to streamline maintenance processes and create a solid organizational structure. It typically includes both upstream and downstream assets, facilitating comprehensive management of manufacturing processes.
Organizations or departments represent the highest level of asset hierarchy, while lower levels capture physical assets like buildings, systems, and their individual components. ISO 14224, initially developed for the petroleum, petrochemical, and natural gas industries, offers detailed guidance on arranging asset hierarchies. Since its introduction, this standard has been widely adopted across all manufacturing sectors, focusing on asset maintainability and reliability.
Having
Why is an asset hierarchy important?
An asset hierarchy helps manufacturers efficiently plan and schedule maintenance activities. By assigning each asset a place within a computerized maintenance management system (CMMS), companies can track individual asset performance, review repair histories, and make informed decisions regarding asset replacement, maintenance budgets, and asset health.
Keeping the asset hierarchy up to date also assists financial stakeholders in identifying which assets are in use and which are idle, aiding in depreciation cost allocation.
Benefits of asset hierarchy
Utilizing an asset hierarchy provides a number of benefits, including:
Improved maintenance planning: An asset hierarchy helps track maintenance schedules and pinpoint the root cause of equipment failures. By using a CMMS, manufacturers can monitor each asset’s repair history, assess its current condition, and make data-driven decisions about replacements and budget allocations.
Enhanced financial planning: Asset hierarchies allow manufacturers to track labor hours spent on maintaining specific equipment. This enables better forecasting of daily, weekly, or monthly overtime costs. Additionally, maintenance technicians can generate work orders tied directly to specific assets, improving inventory tracking, and reducing unnecessary expenses.
Data-driven decision making: With a well-structured asset hierarchy, companies can implement key performance indicators (KPIs) within their CMMS to monitor asset efficiency. This data helps drive corrective actions that improve productivity and overall organizational efficiency
Best practices of implementing an asset hierarchy
The ideal time to implement an asset hierarchy is during a CMMS upgrade or initial implementation. Following best practices ensures the hierarchy is structured for both current and future needs.
1. Establish parent-child relationships
A parent-child relationship in the asset hierarchy helps identify which assets are maintainable and which are components of a larger system. For example, a manufacturing plant might list production lines as parent assets, while individual machines like conveyors and palletizers are child assets. ISO 14224 provides detailed guidelines on structuring these relationships.
2. Create effective naming conventions
Asset naming involves assigning unique identifiers and descriptions to each asset. A clear and consistent naming convention streamlines maintenance workflows by simplifying parts purchasing, inventory accuracy, and repair tracking.
Here are some tips for creating effective and efficient naming conventions:
- Use a simple, clear format (e.g., Organization_Location_System_Equipment_Part).
- Apply a consistent approach across the organization.
- Include relevant details such as location, building, and department.
- Ensure the format can accommodate future growth.
- Follow industry standards, such as ISO 14224.
Here’s an example for “Company ABC.” Under their facilities utilities department, Company ABC has one boiler in the boiler room, which has two infeed valves. A simple naming convention could look like this:

3. Establish the right reporting structure
A well-organized asset hierarchy is crucial for visibility into the current state of assets. Maintenance planners and coordinators need to understand how assets relate to one another to effectively schedule maintenance and prevent disruptions.
For example, if an HVAC unit belongs to a larger asset group and has subcomponents like a motor and gearbox, these relationships should be reflected in the hierarchy. This setup enables technicians to locate the right parts and improve asset performance through root cause analysis and Failure Modes and Effects Analysis (FMEA) during major failures.
Conclusion
Interested in establishing your own asset hierarchy? If so, Brightly’s knowledgeable and experienced solutions consultants can help you by providing specialized support tailored for your unique needs.
Click the link below to book a call with a consultant today.
Request a Demo | Brightly (brightlysoftware.com)