Gain an Accurate View of Asset Maintenance Costs
Learn how a Computerised Maintenance Management System (CMMS) can help you:
- Gather accurate data with flexible and customisable Work Order Costing solutions to suit your business maturity.
- Analyse maintenance costs and failure history against a specific asset or asset class.
- Make better business decisions for the continuing operation of your assets or for capital replacement.
Speakers:
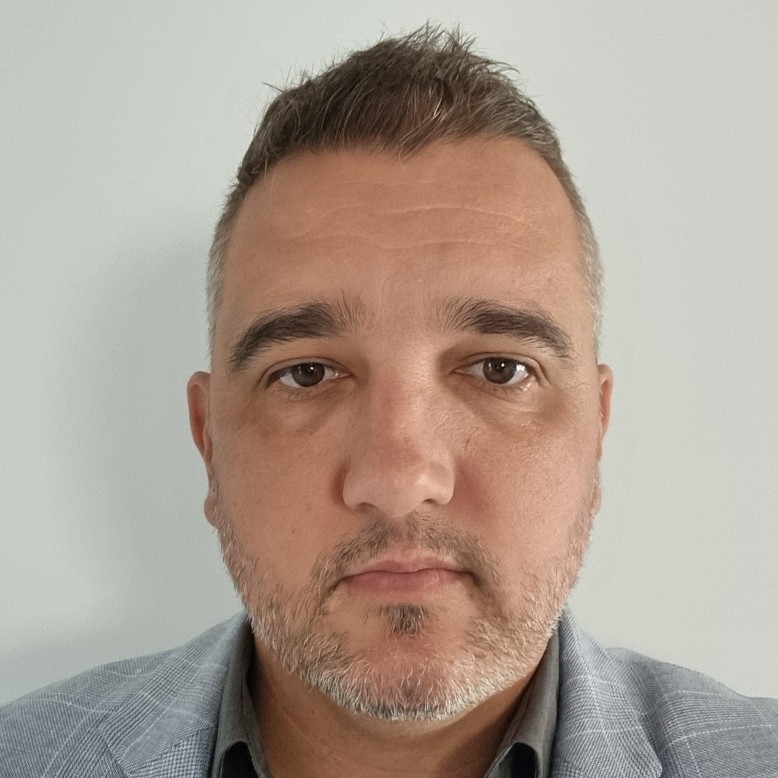
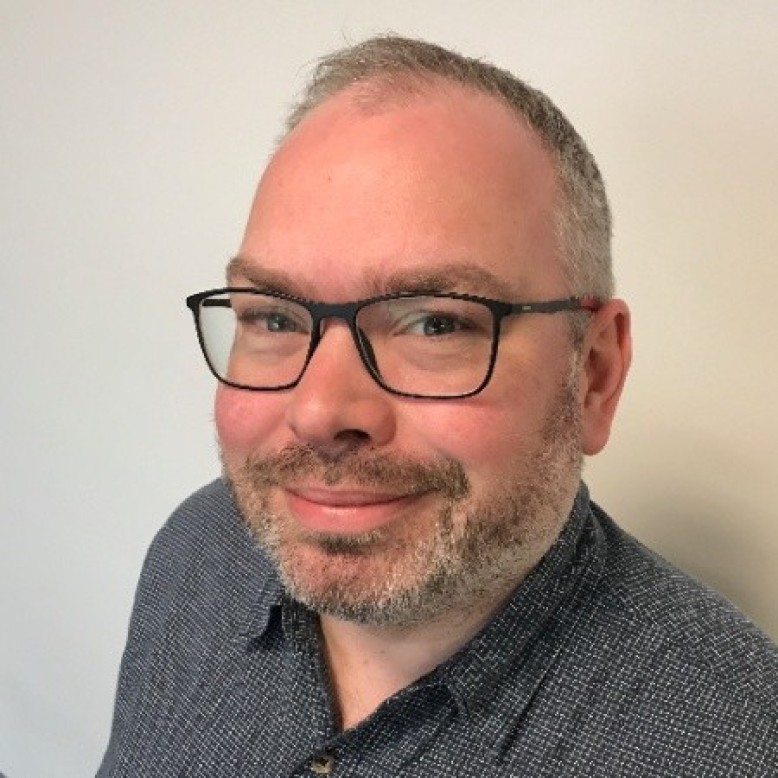
Good afternoon and good morning, depending on where you are. And welcome to our webinar today. So today we're going to be covering off on how you implement a few different things. So first of all, I'm going to be talking about how to broadly how to gain an accurate view of your maintenance costs. So with that, we intend for the webinar to go for around 40 minutes.
So I'll be covering off firstly on the benefits of the CRM, a mess for those that don't know that technology computerized maintenance management system. What's important to understand the cost of your maintenance? And lastly, then the approaches to capture costs. So we're covering off the different approaches that can be implemented and used. We'll finish off the session with a Q&A at the end, So please hold off on your questions to the end.
But please, if you go through, please make note of those questions and there is a little Q&A box you can type those into. So this session will be recorded and you will be sent out the link to download or view this session. We'll send it out after the sessions. Complete. Okay. So in terms of myself. Quick introduction. My name is Christian Melinda, the principal consultant on the implementation team with broadly my bio IDs up on the screen.
So if you want to have a repeat of that, you can go through and you can do that. But yeah, I've worked in the maintenance and asset management industry for quite a while now, so I've implemented quite a few systems with various clients and so on and multiple different types of systems as well. So first of all, I want to talk about the benefits of using a, let's say, a mess.
So first big benefit is being able to track material usage. So by knowing what materials are being used, you can manage inventory levels and more importantly, influence your purchase pricing. So a lot of clients often start out and wondering what goes into a system and what do you get. So that's one of the major benefits. Next benefit, you have to monitor efficiency of your workforce.
So knowing how many hours staff are working allows a better resource control and allocation. You can also then monitor those costs against assets and the locations of those assets to better plan where your work teams are established. So you can even use that data to go as far as planning where you might have depots or or crews located.
So using that data to make those high level business decisions. Our third benefit is cost control. So recording actual spend allows, plus the monitoring of budgets will help reduce overspend. There are some jobs you may need to push back or lower your sales to achieve your budget, or you can increase your service levels if you're underspending in certain areas.
So it gives you a lever that you can pull there In terms of, you know, your cost and the levels of service also identifying underperforming assets. So by tracking costs of work and having this work raised against the asset will allow us to identify the assets which are underperforming or problematic. So can we change the way maybe we're maintaining those assets or do we need to consider a different maintenance strategy?
So that information can lead to those decisions? You know, whether you need to replace that asset sooner or you change that strategy, you start to collect a lot to allow you to make those decisions. Also, benchmarking. So knowing the cost breakdown of your work orders allow you to benchmark against potentially external providers.
So if you're doing your maintenance in-house, you might want to benchmark versus going external.
If you have all the lowest elements cost on your work order, you can see whether you're efficient and competitive against other workforces. Good way to justify keeping your maintenance in-house. So now there's been a big trend, I think noticed a trend lately, particularly in some of the government spaces with a lot of maintenance being outsourced. You wanted to protect your your crews.
That's one way of doing that, speeding up the benchmark continual improvement. So if you're doing all of the above, keep doing them and identify areas for improvement. So by doing all those things that I've just mentioned, you can actually, you know, keep analyzing that data and get better at what you're doing. Okay. So why is it important for us to understand the cost of maintenance?
Okay. So you can say there's an iceberg on that slide. Hope it makes more sense in the next slide. So an assets lifecycle, they can see they've got a little diagram which talks about, you know, your requirements defining what you need and planning to to build. That may be then constructing that asset once it goes through those phases, it goes into your maintenance operations and you're doing some condition and performance monitoring on the asset.
Eventually it will get to the stage where it's up for renewal or disposal. So a long life infrastructure asset typically spends 80 to 90%. They lock in that maintain and operate phase. So that area that we've got circled that end in that that portion of its life, you can accumulate up to 80% of the total lifecycle cost. So that's a huge amount of money in that particular phase of its lifecycle.
So that's what's really important. So as previous, the slide planning in construction costs are just the tip of the iceberg when it comes to the total whole of life cost to maintain and operate an asset. Obviously that may be different depending on what type of asset it is. Some assets may have less in the maintain and operate. Some might obviously accumulate more cost in that phase.
So just want to gauge from the audience here. So what statement best describes how you currently analyze your maintenance costs? So got a few options there. One being, you know, you don't have a system at all, so you do not capture any cost in around what you're doing. Second option of a maintenance system, but not configured to capture costs against an asset.
That option would capture some costs, but they are inaccurate and outdated and probably not analyzed. We do capture costs, however, they are analyzed and possible probably the highest level of maturity. We capture and analyze maintenance costs against assets to inform our strategic decisions. So if you will, 30 seconds or so just to go through and see a few people submitting them now.
Yep, Still a few people clicking. Okay. I think we will wrap that one up there. 60%, 60% of people have responded or sometimes have the answers to those questions. So it looks like the majority there do have some costs captured, but they're inaccurate and outdated. That's not analyzed. I typically see that quite a lot with a lot of the implementations that I do.
We see like, you know, rates in all cost against things. Quite often those are not then maintained in the system.
Things of the moment where you've got no blowouts in material and construction costs, you know, you might need to update your material cost and finding a system more frequently to reflect real world pricing. So that's good to see.
Really good to see. There's 8% still that are doing that full analysis. So well done to those guys. That's great to hear. Great to see. So in terms of the typical cost elements that you would capture on a work order, so Labor, labor is obviously a big thing tracking what type of craft or trade is being undertaken, how many hours and a cost for that materials and parts make up another element and external services.
So you may be bringing in other service providers to do part of your maintenance or you might be hiring inside plant or equipment to also undertake that maintenance so that the typical cost of elements that you would capture or configure when implementing a system to capture on a working. So next time we're going to discuss the different approaches that can be implemented for capturing maintenance costs.
So some of these are dependent on probably the system you use and also your your organization's organization's appetite and maturity around your maintenance activities. So the approaches we're going to talk about today, obviously no capture of costs can be talking about why, while you may or may not do that, the second option will be activity based costing. So I'm going to talk about this a bit more in the next few slides.
You know, write cost of elements and then a fully integrated maintenance system. So when I talk fully integrated, I'm talking fully integrated into stores, payroll and all of those other systems. And when I say unit rate cost and I'm talking about those elements that we just mentioned before, the labor material that are in service. Okay, So I'm talking no cost capture.
So what is the benefit if I have a maintenance system, but I'm not capturing any costs. So obviously there's the reduced data entry. So there's no overhead to capture any information. But what that doesn't give you, so you don't have the ability to monitor and control your costs. So some of those benefits that we mentioned earlier, So are you sustainable or adding value after we measure that?
Are you making the right decisions and making the most of the opportunities to change market strategies and maximize the value that you're getting from your system? Not only your system, your people and your staff and your contractors and all of those things as well. And obviously you've got some limited control of your budget. So maybe having to spend in other ways are reporting out of a finance system to see how much you've spent or, you know, maybe a procurement system reporting on invoice costs and so on.
So there is a bit of disparity there. So this approach may be suitable if your maintenance is outsourced and the management of those assets may also be outsourced. So maybe you just want to recall that something was done. But if an existing maintenance contract is in place and the contractor is already capturing the information, you could possibly amend this approach and capture, say, a total amount for the work at the end of the job and record that on the work audit.
So you could vary that, if you would. Taking that approach would be maintenance and it was outsourced just to capture a cost that would give you some ability to do some kind of analysis. So next option is the activity based costing. So this is a summary. What this be is analyzing UK activities that you undertake for an asset and then define an all inclusive unit, right, for that activity.
So it is a simple approach and will give you a ballpark figure for the work of that work order and the work against that asset. So it will allow you to do some analysis and support some strategic decision making negatives. So it won't capture any specific nuance to that job or asset. So for instance, if I had an all inclusive unit, right, for an activity such as pothole repairs, if I went and fixed a pothole and it just h pothole repair, and one of those is like $300 a pothole repair, I wouldn't actually be capturing if it was a small pothole or a large pothole how many material, you know, how much material was used on that was a half a cubic meter or two cubic meters of mix for that. So I'm not capturing the specific specifics of that job. You're also unable to track and benchmark individual cost elements such as your labor materials for those jobs. And it also has some limited control of budget. So you still have to track spend in other ways.
So you might have an activity based right? You might that system will give you a ballpark figure for your maintenance, however, that might not fully align with your costs and so on, which may be recorded in the financial human system or something similar to that in terms of unit rate cost IT items. So this is having all of your line items configured and captured against a work order.
And so when I say line items, I'm talking unit rights, fee, labor, materials, etc., etc.. So it does allow some detailed analysis to support strategic decision making, the still some negative. So unit rates require periodic review to be relevant. So you still need to to make sure that your unit rate's relevant in that poll before. So a few people in there always like they do have costed elements.
However, they may not have been refreshed, will review current load rates and you may have some cost variations that occur from from unit rates to actual site parts. For instance, if you don't have a continual agreement form for certain prices, they may fluctuate. I'm saying with your external services that you bring in as well, your pricing may vary from your unit rates there as well, but it will give you a very pretty accurate view of what your costs are, very good for you for your decision making.
This approach is often a really good approach. Easy to achieve and easy to implement. So no, I think that's a really, really good approach to get to. And the last approach is the fully integrated C And so when I say fully integrated, I'm talking with your pager system. So you're getting in an actual page all your hours that your rights updated from my job, I'm talking materials as well, integrating maybe with your procurement, so your invoice cost being updated back through that integration onto your work order, getting exact costings.
So this is a really good, I guess that you type in your benefits. It does allow a very detailed analysis to support your strategic decision making. The negatives are a very high level of complexity to implement and your integrations need to be well defined before you start implementing. So knowing what those integration points are and having those well documented and for either of the last two approaches, I find good the activity based stuff anyone new.
Maturity is also a good way to go. Obviously, depending on your organization and businesses appetite. So what do we do with all this data? So data be used for decision making. So if I'm capturing the cost of maintenance tied back to an asset, I can analyze it. For example, may want to periodically analyze my top ten most expensive assets.
So which ones cost me the most with maintain, you know, maybe of a certain asset class, I might be looking at vehicles or whatever it might be looking for those rival problem assets. So, you know, is there a basis for making decisions off that data? Is the data correct? So also are the unit rate unit rates used accurate enough for decision making?
So when would those rates last reviewed? Are they still reflective of real world pricing? For example, I might want to review my change labor charge out rates for the year and compare these to my actual own cost of Labor budget. So I'm not making sure you're in alignment. So doing that periodic review, that was something like my labor rights.
I might want to review them either maybe once or annually in alignment with my budgets and making sure that what I'm actually charging out of my work order in the hours captured somewhat in alignment. So the typical industry standards are usually around sort of 80% of your labor utilization, making sure that you are capturing those hours on your work orders also help you make other decisions around your resourcing that we talked about earlier and what approach to actually take.
So we've got to consider a few things here. So we see the organization's level of maturity. So some organizations are starting from a very low base and may not have the resources to implement fully integrated CMMS. So using something like the activity based costing all the unit right approach work very, very well. Does this add to my want to implement support, my chosen approach?
So some of the best of breed systems support all approaches I'm discussed today were some, you know, fully integrated. ERP requires significant effort to configure and keep running. And the last question around that approaches can I change my approach later as we mature? So making sure that your business in your system can also change with you as you're going along that maintenance journey and I guess improving or looking at ways to improve what you do.
So just want to hand over to yourselves now, see any questions at all. So I've got Darren Burgess here with myself to answer those questions. His bio should be on your screen as well, so feel free to put any questions in the inbox. So I did have a question come through question around how often would you review your material unit rates?
So that's a good question. At the moment, with the changing environment, I would say probably more frequently than you typically would have in the past. Obviously, we've got high inflation. The cost of importing parts has gone up and wait times have gone up as well. So doing that, you'd also have to look at who's managing that data. Quite often in large organizations you might have a procurement branch which holds the pricing for that so that pricing is not integrated into procurement system.
You build managing unit right separately and in your product. You might want to make sure that you're doing a periodic review and making sure that they're in alignment. So you are reflecting those actual costs. Going back to the whole, it seems like there's a few few people that sort of are in that that sort of scenario where your rates may not be as accurate as you want to be.
Christine, we've got a question here as well from Mohammad. So it's asking if this is related to SMP and I presume S&P was referring to standard maintenance procedures. So I think that's in relation to that activity based costing model that you were talking to. Yeah, yeah, yeah. Correct. I would say you've got standard maintenance. Jobs are standard things that you do.
The activity based costing would work well. So I think if you sat down and actually looked at the work that you're maintenance teams did, you could probably write them into certain activities. I know when you go into the maintenance system, we typically do that anyway to record the actual things that you're doing in those tasks so you can break that down for reporting anyway.
So we would typically, you know, say that, yes, let's break those jobs down. Let's look at the cost of elements to that. How much labor would you typically how much time would you typically spend on that? What parts would usually be involved on materials for that and any of those other cost of elements that we talk about and package that all into one, Right.
You view all the questions coming through here as well. Did you want to write the question down? And now I've got another one here. So Bronwyn just asked if she was a little late to these being recorded. The answer is yes. And so we've got a kind of product specific question here. So one of the things we were trying to do this session was to kind of keep it product neutral.
So but, you know, any static system are all the outputs stated today available from its own dashboards or do you need to export to have the Ides do not aquariids Yeah, Yeah. Good question. So we do if you're using the static product, yes, you can build your dashboards around all of those elements. So would you you do have the ability to capture all your parts and material costs.
We services, we will label and you can build your own dashboards around those. You could also look at the water level and get a summary of those broken down by labor, parts, materials and so on. So you can do sort of mid level analysis or you could do the very detailed looking at each individual pottery item and you can set that up on the dashboards.
Now. And I got a cheeky one here from Chazelle who is asking is confirm matter or ascetic and I'll take that one because I worked with both products over a very long period of time. And the answer is it depends what the nature of the organization there requirements and they both got offerings in the maintenance space. So they've got robust mobile products that both got reporting stuff.
So they're both part of our stable and there's so yes, so I'm not going to one isn't better than the other. They they are very similar. Some have will have some will have more things than others. But you'll you'll never draw me on a definitive answer on that. In this we have a deeper conversation on the latest nice diplomatic answer.
And I'm just checking. I don't think I've got any other questions. Although Melissa Conrad pointed out that SMP that Mohammed might be talking to actually is a term for my data. So Alexa esthetic products, which is how which was a maintenance module in my data. So yes, this does it relate to SMP. But you know, at the end of the day, most my data clients who were using SMP have now transitioned to this platform.
So but it is related to what SMP used to do is that instructors lovely or we'll give it one more minute, serve any more questions, come in. Alright. So hopefully today you've sort of seen some of the different approaches that can be taken when implementing a system, you know, doesn't always need to be either. The Big bang, fully integrated approach, you still can get a lot of benefit by even just doing the activity based unit, right?
So yeah, that there are some, some benefits, benefits and negatives of each. But obviously maturity is the big thing. Obviously when you're capturing those those costs and making sure you are actually analyzing them. So even some of the clients I've worked with which are put in large, fully integrated systems, I don't think they're actually getting the value out of the system, but actually doing their reporting and actually viewing the data.
I think that's something that comes with maturity. Once you've implemented and embedded, the use of the system is then actually, you know, bringing specialist people on board to actually analyze and make some great decisions of all, okay, I do have one person coming from another. Darren So there are other Darren's out there, which is is good to know.
So don't ask are both confirmed and static under the brightly banner. And does that mean that both products are now owned by Siemens. So yes, brightly is a wholly owned subsidiary of Siemens and under the bright blue banner confirm and esthetic are both products. They what's interesting about the Australian geography and the APAC area is that both products are in the market whereas for example confirms basis doesn't tell by the accent was originally out of the UK and so there is no static in the UK, so all confirmed in the UK and so we're a bit of a unique geography where yes, both products are lovely or I think we'll just we will finish up there.
So if you'd like to discuss any of these topics from the webinar, please send us an email or contact your account manager. So I want to say thank you all for today. Please note this is one of a series of thought leadership webinars that will be running this year. I next webinar will be held sometime in June and we'll focus on the IFRS 16 lease accounting standard and how to integrate waste management within your asset management system.
So look out for that webinar invite, which should be coming out sometime in July. So I thank you all again, Darren myself, I did have one more question from from Melissa who knows his stuff. So Melissa is asked about just quickly in terms of analyzing the data that we've been talking about, can it support lifecycle modeling? And I think I'll take on some of that.
So as you may be aware, we have a product in our family called Predictor, and certainly one of the key things that predictor there is an input around looking at the total cost of assets. So this is a lot of the focus on the maintenance management, sort of the stuff that keeps the stock running. But then there are those capital interventions that you need along the way.
And if you need to know the total cost of the asset, you need to know both. And one of the key things is, you know, tracking the cost of maintaining an asset at a certain level of service is a really important input to that predictive modeling because it gives you that whole of life costing. So yes, it can be used and it should be used if you're going to do a if you can look at the bigger picture, that's a great question.
But yeah, even some of the inputs into building those models as well, such as looking at lives and so on, of assets. So now by analyzing that maintenance data, you can work out when your assets, we can start to predict when those assets can fail. You obviously build your maintenance strategies around that or one of your strategies might be to renewal replace at a certain point of time before that failure sometimes runs Value may be a valid strategy.
It just depends on the asset and so on. But yes, you can flick some great data in your maintenance model to inform those decisions. So rather than relying on consulting the industry to say a road last amount of years, you might be in a geography where it has a lot of rain and your lives may be shortened because your payments aren't lasting due to the moisture.
So understanding or having that data can get you started can tell you a lot about your assets and how they're performing, right? So thank you very much, everyone. I think that's the last question and thank you. Looking forward to the next session. So thank you everyone. And we'll finish the session then.