Optimizing production uptimes
Meet consumer sustainability expectations
Empower staff with maintenance knowledgebase
Fostering compliance with new regulations
“We use it to consolidate legacy systems into a singular system, so we can use it to better support our maintenance activities,” Welsh says. “We like it because we can take it to a plant and easily configure it for that plant. We don’t have to change the way they do maintenance; we can configure the solution for each plant in the way they already operate.””
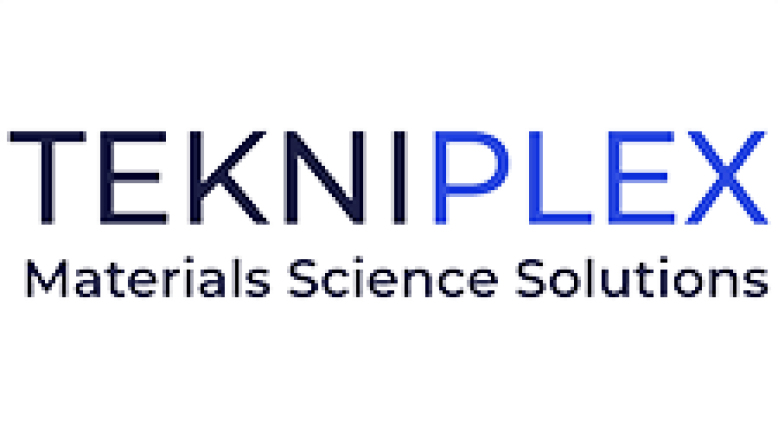
Jim Welsh
Manager of Manufacturing Engineering, Tekniplex
Plastics and Packaging Industry Challenges and Trends
The paper, plastics, and packaging manufacturing industry is navigating a complex landscape marked by evolving trends and significant challenges. On the one hand, there's a clear shift towards sustainability, with a focus on using recycled materials and minimizing waste, necessitating adjustments or upgrades in equipment maintenance to maintain efficiency without compromising uptime. Concurrently, the push towards increased automation and the adoption of Industry 4.0 technologies, such as IoT devices and AI for predictive maintenance, is transforming manufacturing processes. These advancements aim to enhance production efficiency, reduce human error, and preempt equipment failures, thus curtailing unplanned downtime.
In response to these dynamics, a comprehensive maintenance strategy underscored by the deployment of Computerized Maintenance Management Systems (CMMS) is crucial. CMMS solutions not only bolster preventive maintenance efforts but also enhance resource allocation and harness smart technologies for predictive maintenance. This approach empowers manufacturers in the paper, plastics, and packaging industry to boost equipment uptime and operational efficiency, successfully navigating the intricacies of regulatory compliance and sustainability imperatives.
Brightly's CMMS enables proactive maintenance scheduling, ensuring that machinery and equipment used in plastics and packaging manufacturing are always in top condition. This reduces the likelihood of unexpected breakdowns, minimizing downtime and maintaining continuous production flow, which is crucial for meeting delivery deadlines and maintaining product quality.
By automating maintenance workflows and providing real-time access to maintenance records, inventory levels, and work order status, the software streamlines operations. This efficiency not only reduces labor costs but also allows for better allocation of resources, improving overall productivity in the manufacturing process.
Brightly's solutions help identify areas where energy usage can be optimized, contributing to significant reductions in operational costs. By ensuring that equipment is maintained for optimal performance, the software supports energy-efficient operations, which is increasingly important in an era of rising energy prices and environmental consciousness.
The plastics and packaging industry faces stringent regulatory requirements, especially concerning environmental impact and safety. Brightly's software facilitates compliance with these regulations by maintaining detailed records of maintenance activities, safety inspections, and emissions data, making it easier to adhere to legal standards and avoid penalties.
From acquisition to disposal, Brightly's enterprise asset management software provides comprehensive oversight of an asset's lifecycle. This capability allows companies to make informed decisions regarding asset utilization, preventive maintenance, and replacement, ensuring the most efficient use of resources and capital investment over time.
Leveraging the analytics and reporting tools within Brightly's software, businesses can gain insights into their operations, identifying trends, pinpointing inefficiencies, and assessing the performance of their assets. This data-driven approach supports strategic planning, helps to anticipate future needs, and guides investment in new technologies or processes, ensuring the plastics and packaging industry remains competitive and responsive to market demands.
Supercharge asset management with Brightly’s Solutions
Establish asset hierarchies, track maintenance history on assets and prioritize planned work. Generate work orders and submit work request via online portal. Develop PM schedule and track inspections of the assets.
Our world-class strategic asset management, asset health, and capital planning solution provides strategic insight into facilities, assets, and resources that help determine where to focus limited funding.
Optimize resources and save time by removing the need to inspect assets physically with real-time asset conditions through sensor data. Operational parameters like temperature, pressure, and humidity are reported in real-time by Smart Assets sensor devices connected to the assets.
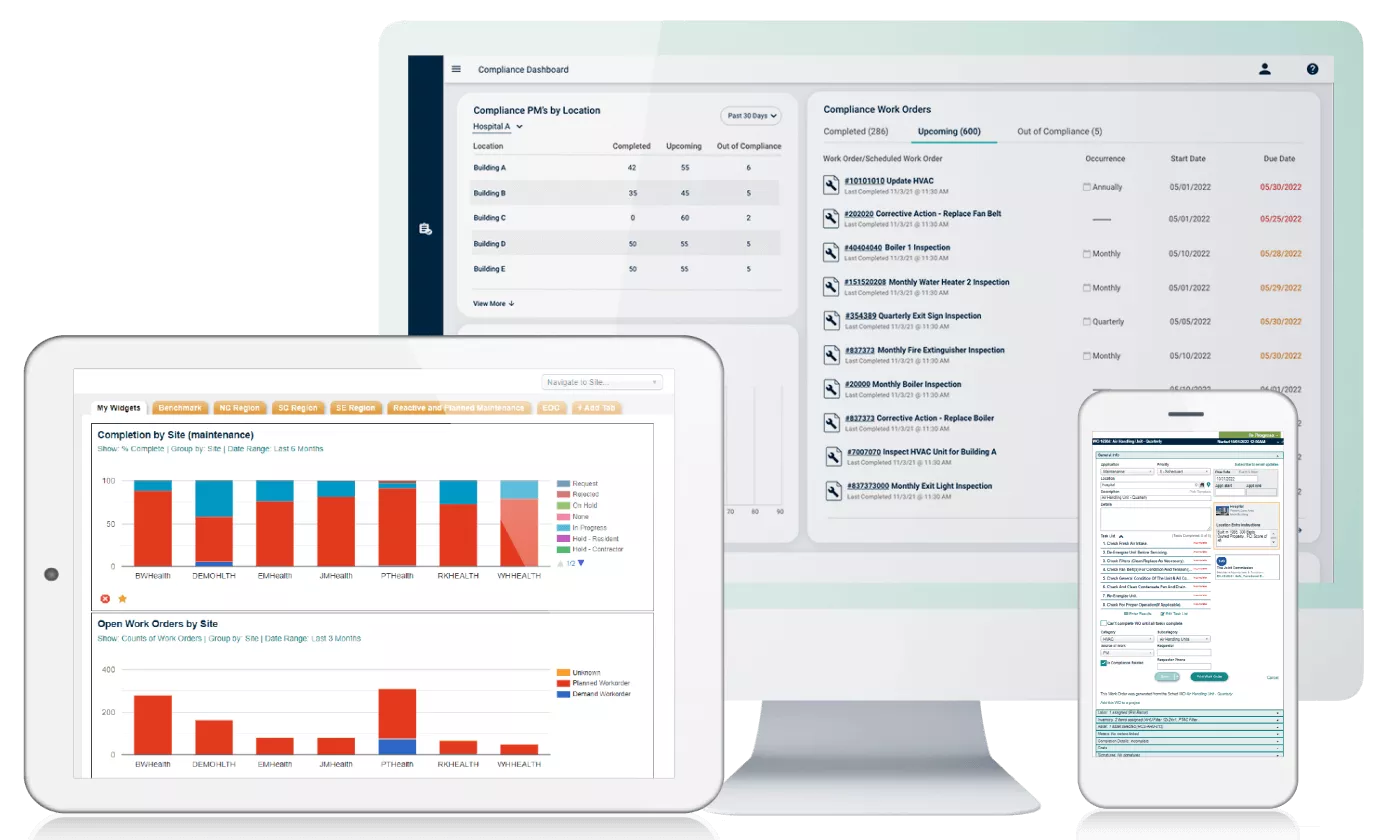
Ready to see how Brightly can simplify your asset management?
Or want to ask a question? Contact Us
FAQ
How does CMMS improve equipment uptime in plastics and packaging manufacturing?
CMMS enhances equipment uptime by enabling proactive maintenance scheduling and real-time monitoring of equipment condition. This approach helps identify and resolve issues before they lead to breakdowns, ensuring continuous production flow.
What are the challenges of implementing a CMMS in an existing plastics and packaging operation?
Challenges may include integrating CMMS with existing systems, ensuring data accuracy, training staff to use the system effectively, and adapting maintenance workflows to leverage CMMS capabilities fully. Brightly provides industry-leading sales and setup support to ensure a smooth process when implementing our software.
Can CMMS reduce maintenance costs for our plastics & packaging company?
Yes! Brightly's CMMS can significantly reduce maintenance costs by shifting from reactive to preventive and predictive maintenance strategies. This minimizes unexpected repairs, extends equipment lifespan, and optimizes labor and parts usage.
Want to uplevel your maintenance and operations?
Let us show you how our industry-leading CMMS can help!