What is Root Cause Analysis?
Imagine your building’s HVAC system breaks down for the third time this quarter, and every fix feels like you’re merely putting a band-aid on a much larger problem. Frustrating, right?
With root cause analysis (RCA), you can get to the heart of the problem and avoid short-term fixes that end up costing you most in the long run. From manufacturing floors to healthcare facilities, RCA is a critical tool for helping maintenance and facilities teams solve problems at their source to keep their operations running smoothly.
What is root cause analysis?
For facilities management teams, root cause analysis helps identify the underlying causes of equipment failures, energy inefficiencies, or recurring maintenance issues. It is a systematic process for uncovering the true reasons behind problems.
Instead of treating symptoms, RCA helps identify the foundational causes of breakdowns and equipment failures so maintenance teams can make more informed decisions around repairs and replacements.
Why is root cause analysis important?
Implementing root cause analysis can save facilities and maintenance teams time, money, and headaches in the long run by:
- Reducing downtime: Fixing the underlying causes of asset and facilities issues leads to fewer disruptions and reduces unexpected breakdowns.
- Solving recurring problems: Diagnosing the cause of malfunctions or breakdowns prevents a continuous cycle of repairs, reducing time waste and increasing efficiency.
- Improving compliance: Understanding issues that could lead to potential noncompliance – such as fire safety, audit failures, etc. – enables facilities teams to more easily plan ahead and ensure consistent alignment with regulatory standards.
3 methods of root cause analysis
There are several effective methods for performing root cause analysis. Here are some of the most popular:
The 5 “Why” approach
The simplest way to get to the bottom of a problem is to just keep asking, “Why?” until you uncover the root cause. By drilling down deep into an issue, it becomes easier to identify what is truly at the heart of the problem.

By continuing to ask “why,” facilities and maintenance teams can uncover issues they didn’t even know existed and ultimately solve problems at the source.
Change analysis
Change analysis involves analyzing at what changes occurred right before the problem began. By identifying shifts in your processes, environment, or personnel, you can pinpoint potential triggers.
For example, if a facility’s energy costs suddenly spiked, a change analysis could reveal that a recent vendor’s maintenance work resulted in incorrect thermostat settings, causing systems to overwork. This approach really highlights on how small shifts in policy or workflows can lead to unforeseen challenges down the line – and enables teams to identify and correct issues early in the process.
Fishbone diagram
This fishbone diagram – also known as an Ishikawa diagram – is a visual tool that organizes potential causes into categories, like Equipment, Processes, People, and Environment. It can be especially helpful for tackling more complex issues.
For example, if a maintenance team is tackling frequent elevator malfunctions, a fishbone diagram might highlight several issues like equipment wear, insufficient staff training, and environmental factors like temperature fluctuations that are causing the equipment to fail continuously.
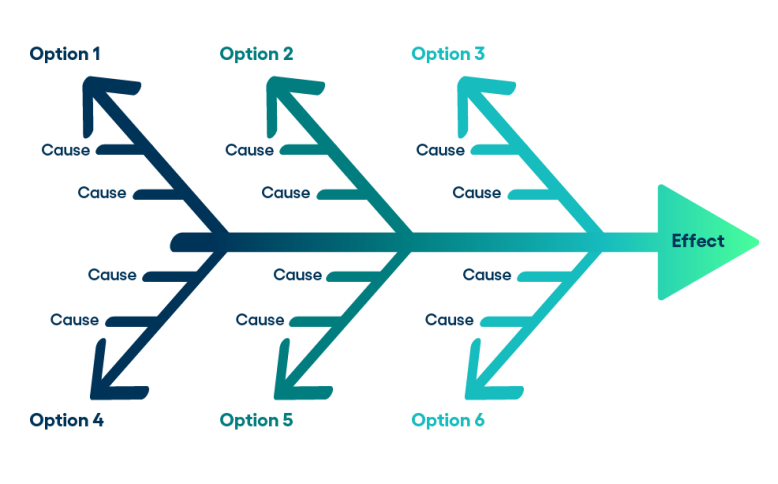
Root cause analysis for asset lifecycle management
Facilities management teams face a number of challenges with maximizing the lifecycles of their physical assets. Root cause analysis offers a systematic way to tackle issues head-on, empowering teams to maintain efficient workflows, simplify decision making, and create longer lasting futures for their facilities, equipment, and infrastructure.
Take energy inefficiency, for example. If your facility's energy costs are spiking, RCA can help uncover the real culprits, such as faulty insulation or outdated equipment. Similarly, if your CMMS data shows frequent repairs on a single piece of equipment, you can use RCA to uncover deeper issues like mechanical wear or environmental stressors that are causing the problem.
Even compliance issues, such as failing a fire safety audit, can be traced back to gaps in staff training, procedural oversights, or missed inspections with the help of root cause analysis. RCA is more than just a problem-solving tool – it’s a strategy for continuous improvement that can enhance operations in any industry or organization where it is applied.
Common mistakes to avoid
Even with the best intentions, it’s easy to make missteps when performing root cause analysis. One common pitfall is stopping too soon. Settling for a surface-level cause without digging deeper can prevent teams from uncovering the real issue causing downtime or equipment failures. For instance, blaming frequent HVAC failures solely on old equipment might cause you to overlook more damaging factors like poor maintenance scheduling, communication breakdowns, or environmental conditions.
Another mistake is failing to involve the right stakeholders. RCA works best when input comes from a variety of perspectives, ensuring no stone is left unturned. Failing to create necessary documentation is another mistake that can lead to failed analysis. That’s why it’s important to always record findings and solutions overtime, to build a knowledge base for the future.
Tools and resources to help with RCA
Implementing RCA doesn’t have to be daunting, especially with the right tools. Computerized maintenance management systems (CMMS) like Asset Essentials are invaluable for centralizing data, tracking maintenance history, and uncovering trends.
These systems enable teams to perform an RCA with confidence, using data to identify and address root causes efficiently. Brightly also offers advanced tools for energy management and sustainability, making it easier than ever to reduce waste, lower costs, and achieve long-term organizational goals.
Take your problem-solving skills to the next level
Root cause analysis isn’t just a method for identifying – it’s a mindset to leveraging data to uncover and prevent bigger issues before they arise. By improving decision-making, reducing downtime, and improving compliance, RCA can greatly enhance operational efficiency.
When paired with modern tools like fault tree analysis (FTA), teams can gain even deeper insights into complex issues. To learn more about how Fault Tree Analysis can complement RCA, explore our recent blog post.